Having started as a wholesaler of packaging made of various materials, PolyER transformed into a polymer-focused manufacturer. Why polymers?
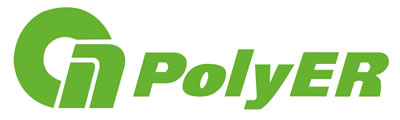
PolyER, a production company, was founded in the Yaroslavl Region in 2000. As of today, the company processes approximately three thousand tonnes of plastic per month, produces 600 tonnes of polymer tape and over 300 million packaging containers. The company's headcount totals more than 500 people, and its production site covers an area of 40,000 sq m.
On the one hand, it was intuition. On the other hand, it was an adequate view of the market. In 1993–2000, we traded in a wide range of packaging products. The materials included cardboard, foil and plastics. So, being in a position to evaluate demand for different types of packaging, we saw the rise of retail chains as a potential driver of the plastic packaging demand. And it played out.
In 2000, we employed a Bilshovyk extrusion machine to begin manufacturing our own polymer packaging. With that equipment, we were able to process up to 60 kg of polystyrene per hour (at the time, we manufactured thermoforming polystyrene sheets for dairy plants).
Today, our key materials are polypropylene (40% of products), PET (40%) and polystyrene (20%). Moulded products and thermoforming sheets account for the bulk of our offering. Each month we make around 300 million moulded products.
What can you tell us about your production site?
Currently, we have 10 extrusion lines and 24 moulding lines. Most of the equipment was sourced fr om Italy or Germany, some from Canada. Since 2008, we have been actively introducing new machines, so now our equipment is compliant with all European quality and efficiency standards.
How did you weather the 2014 crisis?
The crisis did not cut our investments in the company’s development and new equipment. Besides, it was those hard times when we launched our PET business. So, we weathered that quite well. Last year, our revenues grew by ca. 23%, while profit surged even higher.
PolyER site in Pereslavl-Zalessky. Photo: vk.com/polyer_pz.
“Our strong team is what gives us the edge. Each employee is a committed development enthusiast”.
Do you plan to invest that money in further development?
Of course. In 2018, we plan to spend ca. RUB 400 m on this primarily to expand the total area of our warehousing facilities from 10 to 15 thousand sq m. We are also going to launch a new production facility featuring a PET extrusion machine and two moulding lines this year. Those upgrades are expected to ensure double-digit growth at least over the next three years.
What has been the key to the company's success?
Our strong team is what gives us the edge. Each employee is a committed development enthusiast. For example, we manufactured branded plastic tableware as a licensee of the Sochi Olympics. As the event was of utmost importance to the nation, we thought our employees needed to feel PolyER’s role at first hand – and arranged for them to see some of the athletes in action. An opportunity to witness such a success – one that the company has contributed to – is a very powerful motivator for people to strive for professional excellence.
PolyER football team. Photo: vk.com/polyer_pz.
What can you tell us about the new technologies you have tested already?
“Rest assured that goods with our packaging are sold by every major retail chain in all regions across Russia”.
Of course, we aim to use cutting-edge technologies and continuously improve productivity. It is high-speed extrusion machines exclusively manufactured in Germany by our suppliers, such as Battenfeld Kuhne, that give us the greatest performance boost.
Today, we operate four high-speed lines that ensure both robust productivity and reduced energy consumption. Two of them operate in-line, providing for high output wh ere you do not have to switch between products frequently. Most of all, we like to use them for disposable tableware – they can produce up to 6 million 200 ml plastic cups per day, for example. But when it comes to plastic containers, in-line technology is irrelevant, as our versatile product mix requires frequent switching.
PolyER production facility. Photo: vk.com/polyer_pz.
Do you enjoy a significant market presence in Russia?
“We have a zero waste production system in place – we neither dump nor produce waste”.
Rest assured that goods with our packaging are sold by every major retail chain in all regions across Russia.
What goods are those?
A whole lot of things and whatnot. Sometimes we discover it only in stores. Look at this container with croutons, for example – it has a sealing tape. We have found it very interesting.
Fancy that! Snacks?
Yes, rye snacks. This container originates in the Netherlands. We decided to go on with it after we had stumbled on it in Europe. And now our customer uses it to offer these distinctively packaged beer snacks.
Our container products can be divided into two large categories: for manual packaging and for automated packaging using special-purpose high-speed lines. In the latter case, containers must meet very stringent standards in terms of geometry and materials used. This packaging segment has great potential, prompting us to consolidate our position by focusing on quality.
What is your take on the overall situation in the polymer packaging market?
Consumption has been increasing rapidly in some segments. Packaged goods have been proliferating in general, so packaging companies are challenged to extend their shelf lives. The vast territory has been a drag on logistics in this country. In Europe, with its good roads and relatively small size, shelf life is less of an issue.
Does that mean that in the years to come you expect the market to grow?
When I think of the most promising product in our industry, it is, first and foremost, PET with the full production cycle. However, as long as terephthalic acid is imported all the way from China, there will still be room for improvement. I think SIBUR is the company that can get the full cycle going and increase the total PET output. I am sure the market will readily absorb this additional volume – many products need to be packaged.
Will increasing polymer packaging output affect the environment?
We have thoroughly considered this issue. First, we have a zero waste production system in place – we neither dump nor produce waste. Second, we recycle polymers, above all – PET.
That is plastic bottles, right?
Absolutely, we use recycled plastic bottles to produce PET tape and plan to build up the share of recycled materials in our end products.
To what extent exactly can they be used?
In theory, you can substitute up to 100% of feedstock with recycled plastic. However, this requires very clean recycled plastic flakes, and those are virtually unavailable in the market. So now we are limited to 10–15% of recycled plastic in the total volume of feedstock.
What materials do you mainly use?
Our main supplier is SIBUR, we have been cooperating practically since they started producing polypropylene. We were probably among SIBUR’s first customers in this segment, so by now we have built a strong business relationship, reinforced by formula-based supply contracts. We also provide our production facilities to test SIBUR’s new product grades.
A facility tour. Photo: vk.com/polyer_pz.
Are there any particular grades that you would like to see in SIBUR’s product mix?
“Approximately 10% of PolyER products are exported: our destinations are the CIS, Baltic countries and Europe – Hungary, Romania, Sweden, Poland, and Czech Republic. Kazakhstan accounts for about 40% of our exports, which makes it our top destination”.
Overall, we are happy with their product range, with the only exception of special frost resistant grades of polypropylene, which we use, for example, to produce meat packing trays. Polypropylene becomes brittle at low temperatures, so it is not your best choice when it comes to freezer storage. Currently, we ensure frost resistance by using various additives.
How about the quality of the products, are you satisfied with it? Are you planning to cooperate with SIBUR on a larger scale?
Of course we are planning it. It is crucial that we start cooperating with SIBUR on PET, but for reasons unknown to me our offers have so far been declined, even though we are their major consumer and long-term partner. I really hope that this interview will help us start purchasing this type of materials. We are fully satisfied by the quality of supplies from SIBUR enabling us to make products that are in high demand both in Russia and in Europe.
Do you export on a large scale?
Today, approximately 10% of PolyER products are exported: our destinations are the CIS, Baltic countries and Europe – Hungary, Romania, Sweden, Poland, and Czech Republic. Kazakhstan accounts for about 40% of our exports, which makes it our top destination.
Do you strive to actively develop exports?
By all means! Germany is one of the promising destinations we are considering. Unfortunately, European markets are frequently prejudiced about the quality of Russian products and the ostensibly complicated logistics of supplies from Russia. Luckily, in most cases we manage to disprove those myths. Now, we have a task to bring the export share to 20–25%, which is, to my mind, quite feasible.
Download PDF