Building a global zero-waste plastics value chain is not possible unless we engage major materials producers which, along with traditional production, are starting to embrace technologies that involve plastics recycling.
A global vision
At the 2018 World Economic Forum in Davos, James Quincey, President (now Chairman) and CEO of The Coca-Cola Company, announced the launch of a global initiative called World Without Waste. The company’s own efforts towards its vision for a World Without Waste are focused on the entire packaging life cycle (fr om bottle and can production to recycling and reuse) and aim to achieve three goals: make its packaging 100% recyclable by 2025, help to collect and recycle a bottle or can for every one the company sells by 2030, and use 50% recycled material in its bottles and cans by 2030.
CuRe Technology’s solution is called “polyester rejuvenation” technology, and it will allow Coca-Cola European Partners (CCEP) to eliminate virgin PET from its bottles within the next decade
As early as 2009, The Coca-Cola Company introduced a technology that was revolutionary at the time – PlantBottle packaging made fr om 30% plant-based materials. Last year, the solution was made available to any interested party.
The PlantBottle technology is proprietary to The Coca-Cola Company, but other businesses are allowed to use it at no cost. H.J. Heinz was licensed to use it in its ketchup bottles, while Ford Motor Company used the biomaterial in the fabric interior of its hybrid model. In theory, the PlantBottle manufacturing process can be used to produce a variety of other goods, fr om clothing to carpets. The PlantBottle technology is also already used in Russia: AdeZ, a plant-based beverage launched in the Russian market in 2018, uses purchased bio-bottles.
Coca-Cola bio-bottle made using recovered and recycled marine plastics.
However, the company goes beyond proprietary technology development, offering funds to drive innovation around the world. In 2018, Coca-Cola invested USD 15 million in Circulate Capital, a venture loan fund established to address ocean plastics in South Asia and Southeast Asia. In the same year, to provide an additional financial incentive for plastic waste collection, Coca-Cola invested in Ioniqa Technologies, the Dutch company that collects hard-to-recycle plastic and transforms it into high-quality, food-grade PET using technology based on waste depolymerisation. For example, Ioniqa Technologies has come up with a solution to handle polymer wastes of different colours, consistencies and qualities. Coca-Cola explains that these plastics are first broken down to their basic building blocks (monomers), which can then be used to produce high-quality packaging without any material loss or degradation – thus fully reusing old packaging by converting it into new products.
“Using these more efficient enhanced recycling processes we can help reduce the high losses of PET we see in mechanical recycling and because we are reforming the polymer to perform like new every time we go through the recycling process we can truly start to create a closed loop for PET recycling,” explains Scott Pearson, senior director, Global R&D Engineering, The Coca-Cola Company. “Materials that would have been wasted or used to make carpets or textiles can be converted to bottles, again and again.”
Ioniqa is building its first PET plastic upcycling factory in the Netherlands.
Ioniqa Technologies has come up with a solution to handle polymer wastes of different colours, consistencies and qualities. These plastics are broken down to their basic building blocks (monomers), which can then be used to produce high-quality packaging without any material loss or degradation.
In summer 2020, the company financed the launch of CuRe Technology, a Dutch recycling start-up created by a consortium led by the Morssinkhof Group, a Dutch plastics recycling company, and the Cumapol/DuFor Group, a recycling innovator based in the Netherlands, with support from the Netherlands-based strategic partners DSM-Niaga (a DSM innovation venture) and NHL Stenden University of Applied Science.
CuRe Technology’s solution is called “polyester rejuvenation” technology, and it will allow Coca-Cola European Partners (CCEP) to eliminate virgin PET from its bottles within the next decade. The company projects that this will contribute to the overall removal of approximately 200,000 tonnes of virgin PET from CCEP’s packaging portfolio per year, enabling the company to move to a circular economy.
CuRe Technology’s “polyester rejuvenation” technology pilot plant in the Netherlands.
Embrace action
Humans have produced over 8 billion tonnes of plastics globally since the 1950s when plastics started to be widely used, and now the contamination of the planet with packaging waste is a problem that is more acute than ever. The September (2020) issue of Science Magazine ran an article by a large team of researchers from different countries describing five pollution scenarios between 2016 and 2040. According to their estimates, even with immediate and concerted action, another 710 million tonnes of plastic waste will have cumulatively entered aquatic and terrestrial ecosystems by 2040. However, this is still a 78% reduction from the “business as usual” scenario based on 2016 pollution rates. The article’s authors emphasise: To avoid a massive build-up of plastic in the environment, coordinated global action is urgently needed to reduce plastic consumption; increase rates of reuse, waste collection, and recycling; expand safe disposal systems; and accelerate innovation in the plastic value chain.
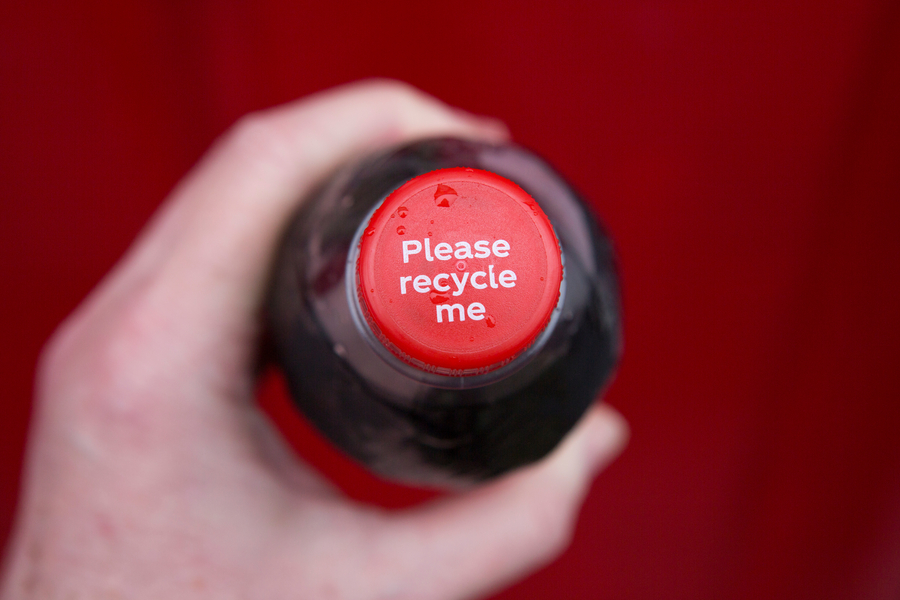
To avoid a massive build-up of plastic in the environment, coordinated global action is urgently needed to reduce plastic consumption; increase rates of reuse, waste collection, and recycling.
An eco-friendly business model
SIBUR is a long-standing partner of Coca-Cola HBC Russia, winning the company’s Best Service award in 2018 and the Supplier of the Year award in 2011.
The green granule production process is projected to utilise some 34,000 tonnes of recycled plastics annually. This process is built around PET flakes, i.e. shreds of used food packaging, which after several stages of washing and cleaning are reused in the virgin polymer production cycle
Every year, SIBUR allocates billions of roubles for projects related to environmental protection and the introduction of environmentally friendly technologies. Last year, SIBUR joined the UN Global Compact. Since 2018, the Company has been a member of Plastics Europe, an association of more than 100 plastics manufacturers which aggregately account for 90% of European polymer production. It also supports Operation Clean Sweep – a PlasticsEurope environmental initiative aimed at preventing polymer particles from entering the environment.
In mid-2020, SIBUR launched a project to modernise its POLIEF site in Blagoveshchensk, Republic of Bashkortostan, to enable the use of recycled content in polyethylene terephthalate (PET) production. In Q1 2022, POLIEF is expected to start producing green PET granules used in packaging for beverages, dairy products, medical products and household chemicals.
The green granule production process is projected to utilise some 34,000 tonnes of recycled plastics annually. This process is built around PET flakes, i.e. shreds of used food packaging, which after several stages of washing and cleaning are reused in the virgin polymer production cycle. The output of this process is a virgin-quality PET granule with stable properties but also recycled content. The solution will allow SIBUR clients to achieve their sustainability goals faster and with no additional costs for packaging production upgrades that enable the use of 100% recycled material.
PET flakes will come to POLIEF from different parts of Russia to supply materials for the project, with Bashkortostan having priority as the host region. The project will rely on intermediates from processed bottles, washed, cleaned and prepared by suppliers at their own sites. Bashkortostan currently collects 4,000 tonnes of used PET bottles every year, but potential capacity is much higher – up to 20 ktpa.
Full steam ahead for POLIEF’s project to launch production of PET with recycled content.
The large-scale adoption of chemical recycling is constrained by the relative novelty of the technology (different solutions are used for different types of polymers), as plastic waste is heterogeneous and scientific research continues to find more effective solutions
This is SIBUR’s first circular economy project, but it certainly is not the only one – the Company also explores other directions to develop polymer waste recycling.
All these projects can be broadly divided into two groups: mechanical polymer recycling projects, wh ere materials are physically cleaned (shredded, washed, filtered to remove unwanted plastics, metals and other impurities, then melted and pelletised), as is the case with the POLIEF project, and chemical waste recycling projects, wh ere the depolymerisation process takes place (the process of converting a polymer back into its constituent monomers or hydrocarbon feedstocks: gas, synthetic oil, etc.).
“We’ve made more progress on mechanical recycling projects, which is unsurprising as this technology is much more mature,” said Sergey Ovsyannikov, SIBUR’s lead circular economy expert.
“But we still see the biggest potential in chemical recycling of polymer waste. SIBUR is a petrochemicals company, so we can use recycled elements in the chemical-synthesis process for new polymers and other organic synthesis products. Moreover, chemical recycling works even with formally non-recyclable solutions, e.g. those used in packaging. These packaging solutions are used to improve the barrier properties of materials and extend the shelf life of products or make the goods stand out to customers. However, as different types of plastics, materials and dyes are used to produce these products, their use in mechanical recycling is very limited, while demand for such products is virtually non-existent. Recyclers in the West even coined the term ‘downcycling’, the recycling of waste wh ere the recycled material cannot be used for its original applications.”
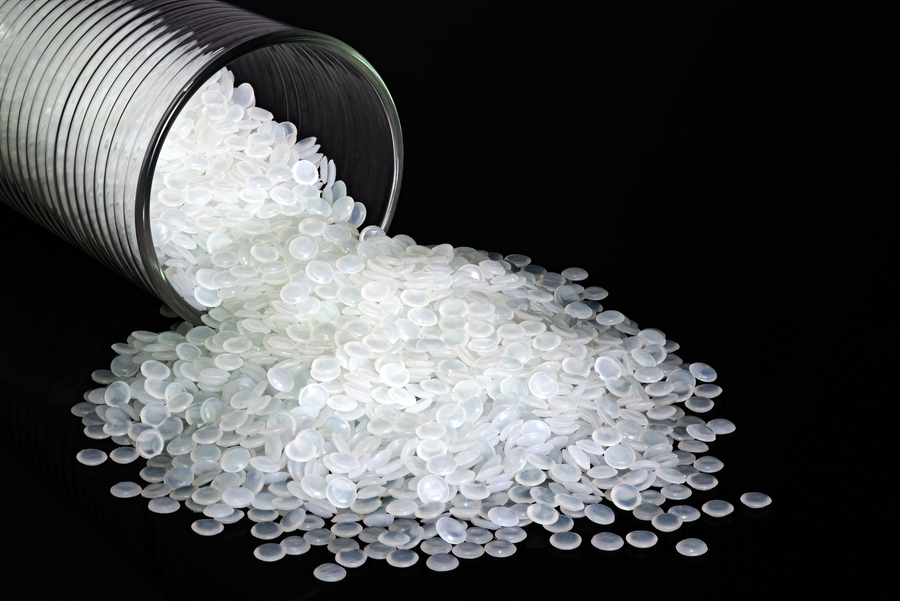
PP granules resulting from the mechanical recycling of polymer waste. Still, chemical recycling holds the biggest potential for SIBUR.
The large-scale adoption of chemical recycling is constrained by the relative novelty of the technology (different solutions are used for different types of polymers), as plastic waste is heterogeneous and scientific research continues to find more effective solutions. We are still in talks with partners and technology companies, and specific agreements are yet to be finalised. “All that can be said with certainty is that recycling is an exciting area and the future lies in recycling complex materials – complex films and highly contaminated plastics. Development in this direction is what market participants expect today,” said Sergey Ovsyannikov, adding that now the team is building feedstock supply chains to support recycling. In his opinion, the least attractive type of waste for the Company in terms of sustainability is production waste. Commercial waste is a good, homogeneous feedstock, but the most sought-after waste today is consumer waste generated by households – this is the most complex type of feedstock mainly collected via regional operators and sorted by the type of product and polymer. And managing this source of waste has been a great challenge in Russia.
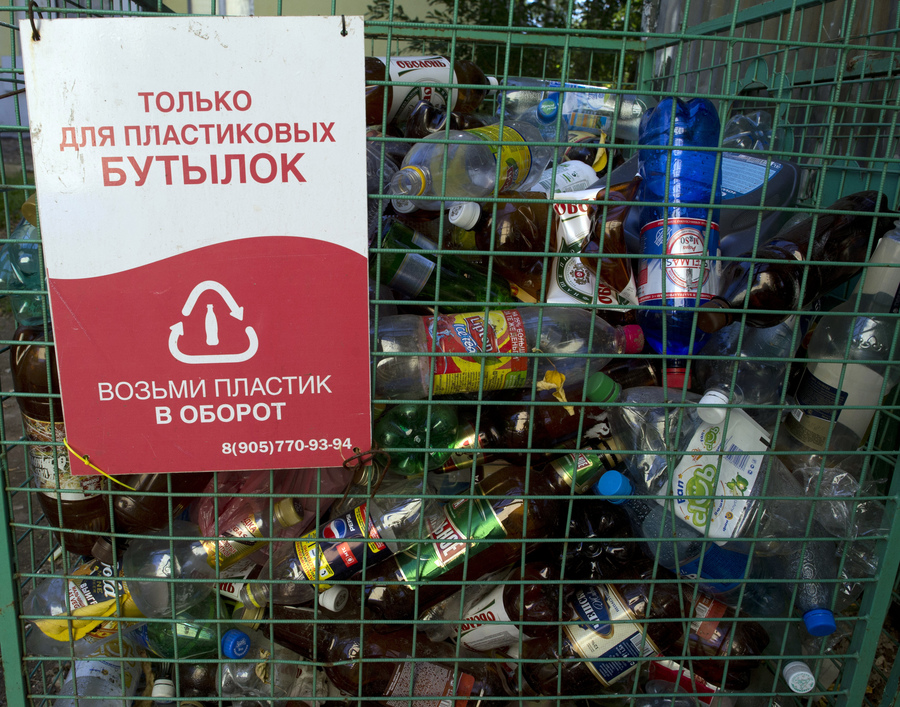
Typically, a number of incorrect items are put into recycling bins for plastic bottles.
Waste management reform and the launch of separate waste collection by citizens has an impact on the collection rates and quality of recyclables, but so far it has not been significant – in any event, such waste is a mixed recyclable in need of additional cleaning and treatment
A weak link
“Efforts to address environmental problems should start by promoting environmental awareness and responsible consumption – instilling the right habits for plastic waste recycling,” said Mikhail Karisalov, Chairman of the Management Board and CEO of OOO SIBUR, speaking at the St. Petersburg International Economic Forum in 2019 (as quoted by TASS).
So far, the collection, separation and recycling of municipal solid waste (MSW) has clearly been a bottleneck in building a zero-waste plastics value chain in Russia.
According to TASS, citing 2019 data from the Solid Domestic Waste journal of research and practice, the amount of MSW generated in Russia annually totals 55 to 60 million tonnes, with organic waste accounting for 40% of the total, paper 35% and plastics 6%. These figures translate into the annual volume of 10 million tonnes of plastic waste and are in conflict with the estimates provided by Russia’s Ministry of Industry and Trade (Minpromtorg), which cited 3.5 to 5 million tonnes last year.
MSW collection operators may discontinue their services due to low payment collection rates among the population.
At any rate, the Higher School of Economics claims that only a small proportion of plastic waste actually gets recycled – between 10% and 15%. This is not enough to keep recycling capacity utilisation high. Due to the lack of a well-functioning separate waste collection system, Russia has to ramp up its imports of plastic waste. According to RBC, which cites customs data, USD 20 million worth of plastic waste was imported in 2018, a 32% increase from the year before.
And most recently, in September 2020, the Accounts Chamber of the Russian Federation warned that MSW collection operators, which serve 15.1 million people across 19 Russian regions, may discontinue their services due to low payment collection rates among the population.
Waste management reform and the launch of separate waste collection by citizens has an impact on the collection rates and quality of recyclables, but so far it has not been significant – in any event, such waste is a mixed recyclable in need of additional cleaning and treatment, noted Mr Ovsyannikov. Here an important step would be, in his view, to implement an effective model for the collection, sorting and disposal of packaging waste within the framework of the extended producer responsibility (EPR) concept introduced in Russia in 2015, as well as certain government support measures for the industry, such as tax breaks for recyclers or scrapping personal income tax for income from the sale of all types of waste and recyclables. He is confident, however, that only a holistic approach can be successful in building an effective waste management industry.
Download PDF