Repair services via video conference calls
In partnership with G-Core Labs, SIBUR’s team launched a joint project in augmented reality to provide remote support, equipment repair and maintenance services. The platform uses RTC (real-time communication) and AR (augmented reality) technologies, as well as the open-source WebRTC (Web Real-Time Communications) standard, which is also often used to develop solutions at Google and Apple. G-Core Labs is famous for developing media platforms for gaming giant Wargaming and their title World of Tanks. Now this team of experts has developed content for SIBUR’s new service, including a virtual table pointer, notification stickers, chat and user groups.
AR platform consists of AR glasses technology integrated with a portal that enables the full digitisation of the equipment maintenance and repair process
Prior to the launch of its own AR platform, SIBUR used the AR Remote Assistance solution from a partner as a workaround that enabled over 300 video calls in 2019 and over 700 online consultations at different plants during the pandemic. Suppliers of equipment, internal experts and representatives of construction companies shared all the necessary information with SIBUR without having to waste time on business trips. Needless to say, remote communication is highly important for an industrial holding company that operates in 20 regions. The pandemic and national lockdown expedited the development of this promising technology: in June 2020, SIBUR launched its own AR platform for remote consulting.
The technology consists of AR glasses integrated with a media platform and enables the full digitisation of the equipment maintenance and repair process. A worker at a plant can connect to a supplier’s representative or internal expert, and a consultant just needs to follow an emailed link to start a video conference call on any device. The service is controlled hands-free via voice commands, so that the worker is able to perform tasks.
Production specialists use augmented reality glasses to make repairs to equipment online.
Anton Fedoseev, the developer of SIBUR’s AR platform, sees the technology’s deep integration with enterprises’ production tasks and universal application on any production site as the new service’s main benefits over rival systems. Igor Klimov, Member of the Management Board, CEO of SIBUR Tobolsk and ZapSibNeftekhim, is excited above all by the financial impact delivered by the technology: “One operational communication session via our AR platform helps save between several hundred thousand and a million roubles by reducing business trip expenses and only needing to pay an expert for a few hours instead of days, all while enabling rapid equipment restart.”
New services provide all necessary information on inventory movement in real time, while digital screens display the warehouses’ operating parameters
Video analytics to drive quality
Within a year, a new video analytics system was launched at SIBUR’s plants in Tomsk, Tobolsk and Voronezh. The service developed in-house has already received positive feedback from production employees and enables savings of millions of roubles. Each site has cameras that monitor the production process and promptly respond to non-standard situations. If an emergency is detected, the smart surveillance system automatically displays the area that requires attention on the screen.
The operator can not only respond to an operational failure but also prevent it as soon as they notice the first signs of a problem. The result is higher operational efficiency, a minimised chance of getting substandard or defective products, no equipment failures, faster repair and maintenance works and thorough control over compliance with industrial safety requirements.
Hundreds of cameras monitor the production process and send alerts in emergency situations.
Vadim Schemelinin, the owner of SIBUR’s video analytics product, believes that a huge advantage of the new service is its interoperability with any video surveillance system. SIBUR’s plants are different in terms of years of construction, location and the specifications of their video surveillance systems. But with the universal software, the Company does not need to purchase new cameras and retrain operators, which can optimise time and financial expenses and help avoid additional stress for employees.
The Company developers are continuously improving the new video analytics system: currently, production sites have several separate video surveillance systems operating at once that need to be integrated with the new service. Another task will be to expand the scope of data collected from sensors to provide a more detailed picture. The archive of records is used to forecast potential failures: video records can be combined with incident statistics and thus used to develop an algorithm to mitigate risks in advance. It always costs less to prevent an accident than to deal with its consequences. Another important strategic goal is closer integration of video surveillance and production lines. Previously, operators could only alert others when they identified a problem, but in the future, they will be able to control lines themselves and promptly prevent incidents.
Each warehouse has an individual set of analytical reports depending on their business process profile
Digital transformation at warehouses
Six of SIBUR’s warehouses simultaneously became part of the digital transformation project based on the SAP EWM (Extended Warehouse Management) solution. New services provide all necessary information on inventory movement in real time, while digital screens display the warehouses’ operating parameters. Vacant and occupied tank capacity in tonnes, pallet space, overdue tasks, the finished product manufacturing and shipment rate, the productivity of shifts by operation type or employees – it only takes a few minutes to read a full rundown of the situation from the figures on the screen. Each warehouse has an individual set of analytical reports depending on their business process profile. For example, the interface of the container movement and loading system at the Tobolsk plants is integrated with the overall vehicle fleet and crane equipment management system. Drivers of container transporters receive tasks with status updates and loading times directly to their tablets.
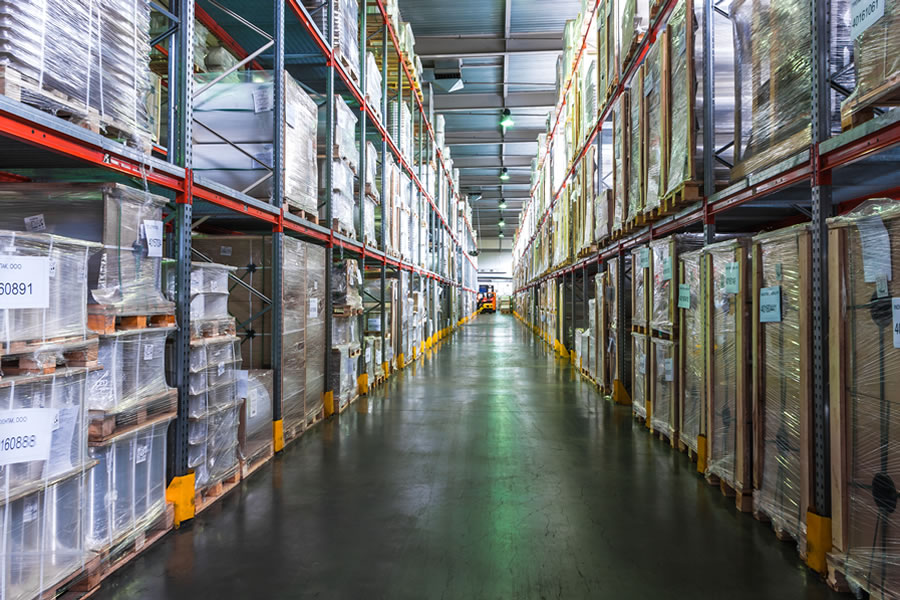
SIBUR’s well-maintained warehouses are unmanned, with digital solutions helping to electronically manage business operations.
The digital transformation project features a single IT solution that covers the specifics of different plants, an enterprise architecture management framework, shared information space and standardised data processing technologies. The single solution enables the Company to roll out best practices and advanced technologies at all key production sites. Alexander Shashkin, Operations Director of a company providing operator services for ZapSibNeftekhim’s container yard, was one of the first to witness the project’s benefits first hand: “Automation has boosted logistics performance and the level of control we have over yard operations: it increased the transparency and controllability of container loading, shipments and acceptance, while reducing crane movement and cutting down the time and costs involved in checking and preparing documents. All of this has translated to a 20% reduction in the train loading and dispatch time (40 minutes on average), which is quite significant for such a major producer as ZapSibNeftekhim.”
To name just a few benefits the digital transformation is opening up for the Company, we are seeing more transparent business process management at warehouses, integrated with production, packaging, quality control and the shipment system. Furthermore, we are leveraging higher manageability and quality planning of warehouse operations, optimising time and cutting operating costs and expenses. Dmitry Prokhorov, Head of Sales and Logistics at SIBUR, is confident that digitisation has been a key enabler for the Company in achieving its strategic business goals: “In the last few years, SIBUR has been actively upping the rate of its digital transformation, since our strong IT focus has been driving the Company’s success in managing its business processes systemically and consistently while achieving its strategic goals in the most efficient way and maintaining its strong position in a changing environment.”
Download PDF