Now, more and more entities support the ESG agenda. Climate risk management is being embedded into processes of global corporations. Russian chemical and petrochemical companies willingly implement initiatives aimed at minimizing their impact on the environment and climate.
According to the BCG report ((based on the polling of nearly 1,200 heads of operational divisions of the world’s manufacturing companies), more than 75% of participants said that carbon neutrality is either the most crucial or one of the top 3 initiatives for their companies. Experts note that corporations may implement win-win strategies helping to both preserve the environment and increase value.
BCG experts note that corporations may realize win-win strategies helping to preserve the environment and increase value
The Managing Director and BCG Partner, Head of the Expert Board in the oil and gas industry in Russia and CIS countries, Kirill Tuishev says, “The biggest petrochemical and oil and gas companies are reviewing, in detail, their carbon footprints and setting quite ambitious goals, since a reduced environmental impact is deemed by many governmental and international regulators as a necessary condition to increase or even maintain investments.”
Nowadays, there are a variety of solutions to minimize the manufacturing impact on the environment. This means improvements in the production efficiency, recycling, and reusing or disposing of waste. This also includes the efficient monetization of methane and co-produced gas, transfer to low-carbon energy resources, storage and disposal of carbon dioxide, reduction of greenhouse gas emissions through investing into forestry and land use based on regenerative technologies, and maintenance of carbon awareness across the supply chain with the requirements to vendors and clients to lower their carbon footprints.
“A priority task of the global oil and gas industry is to lower the manufacturing impact on the environment. Various governments solve the issue in different ways, yet there are common trends, three of which we would like to mention here: switch to renewable energy sources and biofuel, and the resulting progress in bioenergy; decarbonization of the core businesses to decrease the carbon footprint and supply chains; and diversification of raw material businesses (for instance, to natural gas conversion). These three trends could be seen in both the existing projects and long-term strategies of the biggest Russian companies of the oil and gas as well as associated industries,” says Anton Kosach, Managing Director and Partner of BCG, Member of the Expert Board in the Power Industry.
“We can see that the biggest Russian manufacturers are interested in promoting the closed-loop economy, eagerly implement environmental initiatives, and openly discuss sustainable development. Several complementing trends should be noted: firstly, low-carbon plants are being singled out as separate businesses, which will certainly facilitate their progress; secondly, manufacturers are developing and implementing certain measures to make their productions cleaner; thirdly, businesses are cooperating with government in developing standards and solutions to preserve and restore the environment. In addition, major oil and gas manufacturers are either taking part in or initiating eco-compensation measures: developing carbon farms, plant forests, and managing projects to lower climate risks. Investments into the decreasing of carbon footprints of heavy manufacturing will benefit our companies in their sales negotiations with European consumers,” adds Kirill Tuishev.
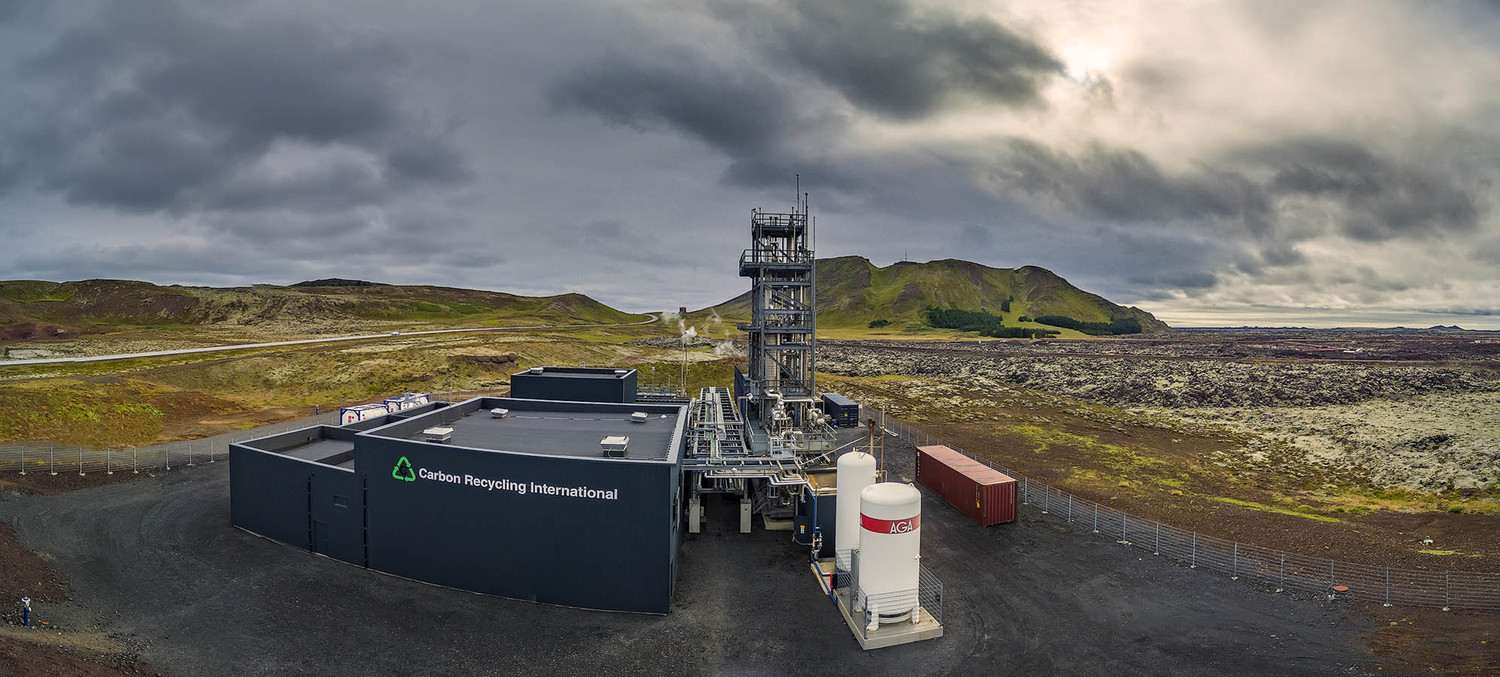
Carbon Recycling International (Iceland) developed a method to simplify the transformation of CO2 into methanol. Photo: carbonrecycling.is
Decarbonization: perspective solutions
Companies can collect carbon dioxide emissions as a by-product of production processes to use it as a standalone product or as a commodity for further processing. This also results in the fact that they are no longer emitted into the atmosphere. BCG experts present successful international cases.
For example, ThyssenKrupp Steel (Germany) intends to reuse CO2 through its innovative technology named Carbon2Chem. This technology transforms gases generated by steelmaking processes into basic chemicals. These can be used for the production of fertilizers, plastics, and different types of fuel.
Meanwhile, Carbon Recycling International (Iceland) has developed the solution to simplify the transformation of CO2 into methanol by direct hydrogenation of collected emissions. The company intends to widely deploy and commercialize its solution in the chemical industry.
Across the globe, shareholders have become more focused on their companies’ ESG policies. According to the Central Bank of Russia, EU plans to introduce carbon taxes on carbon emissions, which may affect more than 40% of the Russian exports, thus costing up to USD 5 billion annually. The detailed EU plan is expected to be announced next month. it may be introduced partially in 2023 and entirely, in 2025. This has forced Russian companies to think about reducing their carbon footprints before the regulations come into effect.
At the same time, for Russian producers, the tendency towards building new and upgrading current plants, by means of installing high-end equipment and implementing technologies that reduce the carbon footprint tenfold is very promising in the field of environmental protection. SIBUR’s fully-fledged ZapSibNeftekhim and Amur Gas Chemical Complex currently under construction, as well as the active rollout of modernization measures, provide good examples of such decarbonization investments.
SIBUR announced its plans to compensate part of its emissions through the potential of Russian forests. The company announced that it is considering initiatives aimed at greenhouse gas emissions compensation that would use measures for increasing the absorptive capacity of ecosystems, including the purchase of carbon units from such projects.
Acting in accordance with the plans mentioned above, SIBUR, together with its partners, began to establish carbon stations in the Tyumen and Voronezh regions. At the stations, researchers will be able to develop the most efficient carbon-storing combinations of plant species and breeds for varying ecosystems. The company also intends to raise awareness of innovative activities and solutions aimed at increasing carbon storage by forests, as well as to cultivate eco-friendly attitudes.
Carbon farms are an efficient tool for storing carbon dioxide.
Reducing the carbon intensity of production and thus improving the environment, could be achieved through replacing obsolete technologies with the advanced, eco-friendly and resource-saving ones
“The domestic chemical industry has strong incentives to progress in consideration of all current goals of sustainable development, including СО2 requirements, and shape most promising trends in manufacturing, as part of both governmental programs and inhouse green initiatives”, says Maria Ivanova, First Vice President of the Russian Chemists Union. “The projects widely supported by the chemical industry include the network of carbon storages to develop innovative solutions and prepare initiatives and new regulations. It is significant that the planned carbon storages would unite governmental agencies, academic circles and industries.”
Emission of harmful substances: innovative solutions
Reducing pollutant emissions and thus improving the environment could be achieved through replacing obsolete technologies by the advanced, eco-friendly and resource-saving ones. And the Russian businesses provide a lot of examples.
Titan Group has established its objective in reducing its environmental footprint. In 2019, the Group began to update its isopropylbenzene processing with the best solutions available, thus reducing up to 85% of its impact on the environment caused by various harmful substances. The Group has also renovated its plants for phenol and acetone. The phenol unit is a unique one in Russia due to its activated-carbon filtration for emissions, which is deemed the most efficient one. In addition, the isopropyl alcohol process has been adjusted to minimize the environmental impact.
“Since we updated the isopropylbenzene processing, we have managed to completely exclude, from our emissions, the aluminium hydroxide which is extremely hard to dispose of in an eco-friendly way,” says Alexey Obukhov, Vice Director for Legal, Titan Group. “We replaced all obsolete pumps with pumps which have a double terminal seal. Previously, small emissions into the air were possible during pumping, now they are absent.”
In 2020, PJSC KuibyshevAzot spent RUB 5 billion on environmentally friendly solutions and managed to reduce its air emissions of various types by 6.7% year-over-year. This was achieved through the refurbishing and updating of plants producing nitrogen acid, ammonia, fertilizers and caprolactam. Currently, the company continues to construct a new unit for ammonia nitrate granulation and evaporation. Its commencement would reduce air emissions by 200 mt per year. The project costs RUB 3.5 billion.
PJSC TogliattiAzot continues the construction of the third urea unit which will become more eco-friendly due to its granulation tower with innovative pollution control equipment. The purpose of the new design is to collect production dust so as to prevent it from getting into the atmosphere. Through this, more than 93% of the granulation tower emissions would be recovered. Moreover, its innovative filtering elements do not require replacement, only cleaning from time to time. In addition to the environmental task, the pollution control equipment also has an economic one – to recover urea dust and reuse it in the production chain.
Titan Group has established its objective in reducing its environmental footprint. In 2019, the Group began to update its isopropylbenzene processing with the best solutions available, thus reducing its impact on the environment by up to 85%. The Group has also renovated its plants for phenol and acetone
SIBUR Kstovo is implementing a large-scale program to update its eco-infrastructure. As part of the program, the closed flaring system is designed, which, upon its commencement, would reduce the plant’s air impact by more than 50% and locally solve the smoke burning issue at the plant. After commissioning the flare system, the facility will be able to burn, safely and without fumes, up to 390 tons of flare residue per hour. The new package is safer and more economical than the traditional mast flares; such packages can even be operated in residential areas, and this particular package will be located at the plant site.
Maria Ivanova, Senior Vice-President of RCU: “Companies of chemical and petrochemical industries are fully involved in making both their facilities and their products environmentally friendly. This is not merely due to a token compliance or following contemporary trends, but rather because of the high responsibility of visionaries who deploy progressive technology to drive major changes in a common cause and take leadership in future development.”
Water: upgrade of treatment systems
Apart from atmospheric emissions abatement, it is necessary to stem the impact on water ecosystems: to reduce clear water intake, implement closed water circulation systems, and reduce the discharge of pollutants.
Among the world practices, Finland has achieved great success in the sustainable use of water resources. This country is a leader in wood processing, the pulp and paper industry, chemical products and materials, which carries a high environmental impact posed by significant quantities of discharge.
Since the mid-1980s, Finland has been actively building biological treatment facilities, which resulted in a decrease in environmental stress due to the effluents discharge. Most of all, this has reduced organic matter and suspended solids content. Contemporary aerobic and anaerobic treatment methods utilize microorganisms which break down organic matter into smaller components.
In addition, the use of membrane filtering technology for water treatment at some facilities allowed for water recycling and considerably lowered their water intake. There are improvements due to more efficient consumption of reagents, sorbents, filters, etc. Simultaneously, the search is ongoing for deep water treatment solutions to deal with heavy metals pollution.
Galina Christoforova, SIBUR’s Head of Environment Department, maintains there are currently two major areas for waste water management. The first one is compliance with the legal environment protection requirements, including stricter control of effluents discharge, abnormal effluents discharge, organization of adequate water supply systems, and the upgrade of treatment facilities. The second one is the use of best practices, including full transformation to a closed-circuit production.
Biological treatment facility at SIBUR-Chemprom.
Biological treatment is widely used in Russia. High contents of organic matter in the effluent make it a breeding ground for bacteria. A state-of-the-art treatment facility using this technology has been operating at SIBUR-Chemprom Perm facility since 2018. Effluents first go through mechanical and chemical treatment, and then live microorganisms join the process. This system allows the lowering of organic matter content in the effluents by 12 times.
High contents of organic matter in the effluent make it a breeding ground for bacteria. A state-of-the-art treatment facility using this technology has been operating at SIBUR-Chemprom Perm facility since 2018
There has been an improvement of a treatment facility at Nizhnekamskneftechem (this production facility will be part of joint operations of SIBUR and TAIF following a merger). The effluent treatment facility at this operation is used not only for its own effluents, but also for the waste water from the local industrial hub and the city sewage. Sand and debris are removed from the effluents prior to biological treatment. Even the smallest debris particles are removed by using a 5 millimeter mesh. This conserves most of the household organic matter, which increases sludge content in the aeration tanks (water tanks for mixing effluents with activated sludge for biological treatment) and improves the quality of biological treatment. As a result, the treatment discharge has a much lower content of iron, aluminium, sulphates, phenols, formaldehyde, and methanol.
“Strong environment protection is among the top priorities in our company,” says Ayrat Safin, General Director of Nizhnekamskneftechem PAO. “That is why we heavily invest in the environmental programs.” Nizhnekamskneftechem is set to invest a record RUB 12 billion into improving the environment in Tatarstan.
Maintaining water quality in large water basins is a priority for petrochemical companies. Under a cooperation agreement with Rosprirodnadzor, SIBUR is implementing a comprehensive environmental safety program. As of today, 5 out of 7 steps in this program have been implemented: treatment facilities have been constructed or upgraded in Kstov, Perm, and Tobolsk, and flare systems have been installed in Perm and Tobolsk. Over the last decade, total environment protection investments of the company measured RUB 23 billion, and about half of that amount was spent to improve the effluent treatment quality. This allowed for the lowering of effluents discharge by 30,000 tons over the last 7 years (a 51% reduction), along with a 65% increase of the annual production.
Taking water samples after all treatment stages at the POLIEF plant’s treatment facility.
Advanced technologies for spill cleaning are used in the low-tonnage chemistry field. “We have a whole function which can be called “hi-tech and ecological chemistry”: we manufacture reagents for water treatment”, says Irina Vendilo, General Manager of the Roschimreaktiv association
“Input of environmental programs implemented by chemical companies in improving the condition of water basins is quite tangible,” says Igor Lyashkov, an expert from the Russian Environmental Movement, Deputy Director at FGUP NTC Chemvest of RF Ministry of Trade and Industry. “For many companies, participation in the projects to restore a healthy river environment is not only an important environmental and social responsibility, but also a way to uphold a positive image,” he says.
It is important that there are advanced technologies for spill cleaning and in the low-tonnage chemistry field. “We have a whole function which can be called “hi-tech and ecological chemistry”: we manufacture reagents for water treatment”, says Irina Vendilo, General Manager of the association Roschimreaktiv, “We have a department in our Low-Tonnage Chemistry science center that specializes on customer support. This support includes analysis of the water in the industrial water collection cycle of a particular facility, and a large number of facilities, including experimental production facilities for optimal reagent dosage selection, that maximally decrease the amount of sewage and treat it as much as possible”.
The innovative solution used is fluorescent tags (molecules that are attached to an object that needs to be monitored), that not only help dose reagents exactly in the amount necessary to support the required amount in the water collection cycle, but also significantly decrease sewage and the amount of neutralizing agents used.
Secondary Use of Waste
The petrochemical sector has a lot of potential in the development of a closed-loop economy, including due to the properties of polymer products, and its recycling for use in production.
In this regard, one anticipated project in Russia is the production of the “green” plastic granule containing recycled materials at the POLIEF plant in Bashkiriya (part of SIBUR). The line is expected to be commissioned in 2022. The company plans to introduce 30,000 tons of secondary materials in the production loop per year. Part of the waste will be collected in Bashkiriya. Currently, there are 4,000 tons of plastic bottles collected per year in the region, but after implementing measures to increase collection and sorting, the potential amount might reach 20,000 tons.
The plastic granule produced could consist of up to 25% secondary materials. This way, the company’s clients get a solution that lets them specify that their goods’ packaging is partly made of secondary materials. This becomes important because, with the transition to a green economy, where secondary materials and solid domestic waste are used as raw materials, the business model changes both for manufacturers and their partners. SIBUR also continues its R&D work which aims to increase the amount of secondary plastic in the granule without losing quality.
SIBUR’s new policy for the closed-loop economy sector and decreasing climatic load hereinafter, “the Policy” - ed. note is an important event in the journey to sustainable development. SIBUR has become the first Russian company to implement such a document.
One of the latest events on SIBUR’s polymer products market was the launch of a number of polymers under the Vivilen brand. It contains a number of solutions for blow molding, injection molding and heat-shrink film production. The new brands of polymers were developed by SIBUR’s PoliLab research center and have been tested using the capacities of recyclers.
“By collaborating with leading participants of the waste management market, we are developing a closed-loop economy and are contributing to decreasing waste that needs to be buried. This is part of SIBUR’s strategy in the sustainable development field”, says Chairman of SIBUR’s Management Board, Dmitriy Konov.
Download PDF
Anton Kosach
Managing Director and BCG Partner, Member of the Expert Board in the Power Industry:
“A priority task of the global oil and gas industry is to lower the manufacturing impact on the environment”.