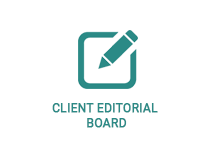
On 15 January 2021, Deputy Prime Minister Yury Borisov chaired a meeting discussing the possibility of using polymer pipes in the oil and gas industry. It brought together representatives of the oil industry, producers of polymers, pipe products and executive authorities, and resulted in tasking Rosstandart (led by the Russian Ministry of Industry and Trade with participation fr om the Ministry of Construction, Housing and Utilities, federal supervisory authorities, and manufacturers and consumers of polymer pipes) with forming a working group, compiling a list of regulatory and technical documentation, and setting out roadmaps to completing the development and implementation of all regulatory documents in 2021. Maxim Kovyazin, CEO of POLYMERTEPLO Group (part of POLYPLASTIC Group), Sergey Shalyapin, Head of R&D Department, POLYMERTEPLO Group, and Pyotr Titov, Director of Information Policy and Development Department at POLYPLASTIC Group, explained why the state is pushing for the use of polymers at oil and gas production facilities, how large the market is, and how the use of plastic pipes will affect the economics of hydrocarbon production.
Why has the use of polymer pipes in oil and gas production become such a hot topic for Russia? They are no new invention, but the state is pushing through the adoption process – they literally gave one year to do it.
Maxim Kovyazin (MK):
The use of polymer pipes in the Russian oil and gas industry has been of interest for a while. Polymer products have been successfully used in gas supply, utilities, sewage and other industries for decades. Various domestic companies, including our own, carried out targeted rollouts of polymer products at the production facilities of upstream companies. But for a number of reasons, the industry remained closed off for polymer pipes. Now, several factors have lined up.
One of them is the launch of ZapSibNeftekhim. SIBUR has been behind the development of various areas of the polymer business for a good number of years. The introduction of a large volume of basis polymers to the market changes the old order: new grades of raw materials appear, and then the question arises as to how they can be used in the national economy. That isn’t even mentioning import substitution. Russia seeks to not only extract and export oil and gas, but also to deepen their processing. Manufacturers of polymer products have become stronger. With the advent of support in the form of SIBUR, companies that produce polymer pipes have become more vocal about their own problems and development paths. All in all, this resonated with the government – they have heard us.
Sergey Shalyapin (SS):
Don’t forget about the economic side of things. High oil prices stopped people fr om questioning the cost of metal pipe, and from paying attention to corrosion resistance, installation costs and service life. That is, until 2020 changed everything. The price of oil fell, and metals continued their multi-year trend upwards. The industry was faced with the need for new, cost-effective technologies. Environmental safety, reliability, cost reduction, and lifecycle cost have come to the fore. Polymer solutions are highly relevant for oil and gas companies, which, by the way, they themselves stated during the meeting with Deputy Prime Minister Yury Borisov.
What benefits do polymer pipes have over other materials?
MK:
There are plenty. For example, their service life is 20–30 years or more (depending on the requirements and parameters), while metal pipes serve for 5–7 years. What’s more, installation is faster and cheaper. I’ll give you an example. Let’s take 1 km of pipeline with a diameter of 110 mm: if it is a metal pipe, it will need 84 butt joints, 25 minutes for each joint, highly paid employees with relevant qualifications, electrochemical protection, and so on; when working with a flexible polymer reinforced pipe, you only need five connecting fittings, and the crimping time of one connection is 10–15 minutes. The complexity of process operations is much lower, and so are the costs.
Up to 70%–80% of the consumer’s expenses are in the operation of the pipeline. Meanwhile, the cost of the pipe system makes up 10%, and design accounts for another 10%. If you take into account the fact that metal pipes need to be replaced more often than polymer pipes, the amount of savings increases by an order of magnitude.
The main benefit for the consumer is the reduced cost over the entire product lifecycle. We estimate savings of 30% or more, but much depends on the industry, region, and other parameters.
When installing pipelines, flexible reinforced pipes have benefits over their metal counterparts.
Pyotr Titov (PT):
You can gauge the impact by looking at areas wh ere there has already been an explosive growth in the use of polymer pipes: in gas distribution networks and water supply. Over the many years that they have been in operation, we have built up sufficient experience and data on economic efficiency. In one of his speeches, President Vladimir Putin drew attention to the fact that the costs involved in operating utility networks using polymer systems are almost cut in half. And if you remember that the service life of polymer products runs into the decades – and maybe even centuries – the actual savings are higher still.
What are the restrictions on the use of these kinds of pipes? They can’t completely replace their metal counterparts, can they?
MK:
This question doesn’t really apply to tubing, casing and trunk pipeline systems. In terms of physical, mechanical and chemical properties, polymers are not yet applicable there. We are talking about process pipelines that are deployed in oil fields and quickly wear out. Reinforced polymer pipes can certainly replace metal pipes and reduce construction and maintenance costs.
SS:
The characteristics of polymers themselves lim it their spread. For example, pressure: the maximum safe level for reinforced polymer pipes is 210 atmospheres. This would be useful for water pipelines in reservoir pressure maintenance systems, and are currently at the R&D stage. A pipe with a working pressure of 150 atmospheres is currently being tested at a LUKOIL site. Basically, we are looking at 40 atmospheres. At this kind of pressure, reinforced polymer pipeline systems can operate normally for 15–20 years or more.
Polymer products have been successfully used in gas supply, utilities, sewage and other industries for decades
The next restriction is temperature: the operating temperature range of polymers is significantly lower than that of metals. In some cases, thanks to the use of cross-linked polyethylene and high-temperature polyethylene, we can reach about 100–115 and 75–85 degrees, respectively, but the general temperature range is 40–60 degrees. The maximum diameter of flexible, reinforced polymer pipes available for oil and gas fields is 150–200 mm. They are restricted by the dimensions of the transport drum, the maximum diameter of which shouldn’t exceed 4.5 m when being transported on the back of a special vehicle across bridges at transport infrastructure facilities. Reinforcement technology makes it possible to produce larger pipes; however, due to restrictions on the dimensions of the drum, they can only be made in segments of no more than 12 m in length if they are being transported by the classic transport modes – road or rail. In this case, the consumer’s gains are lost when installing systems, as the number of joints increases.
PT:
A number of restrictions apply to the use of surface pipelines. Polymers are sensitive to UV radiation, so special stabilisers are added to the polymer, or protective coatings are applied to the final product. In a number of regulatory documents, there are requirements for so-called “zero flammability”. The term is quite controversial, as going by the regulations, polymers objectively do not possess this property. Although today, polymer piping systems are even used in fire sprinkler systems.
Large diameter pipes are manufactured at POLYPLASTIC Group’s Novomoskovsk plant.
How should the regulatory framework change so that polymer pipes can compete with metal pipes in the oil and gas sector?
SS:
Despite the fact that the USSR has long ceased to exist, the domestic economy continues to rely on its GOSTs and standards. If your products don’t comply with them (or are unregulated), they won’t achieve mass adoption – and not because of a ban. End users won’t understand what operational parameters the product has and how they should be evaluated, designers don’t know how to design facilities or equipment using it, regulatory authorities don’t know how to assess compliance and quality, and so on. There is no regulatory framework for the use of reinforced polymer pipes in the oil and gas industry yet. Manufacturers and consumers have previously made attempts, but now there is a consolidated desire to solve this problem. Moreover, it isn’t even that difficult, although it requires a significant amount of time and organisational efforts.
In one of his speeches, President Vladimir Putin drew attention to the fact that the costs involved in operating utility networks using polymer systems are almost cut in half
Oil and gas companies in North and South America and the Middle East have been using polymer pipes for decades – their share in the total volume reaches 40%. The world has accumulated enough experience in this area: it is reflected in many regional standards, which can become the basis for national ones. Polymer pipes have been used at Russian oil and gas facilities. The groundwork for the development of national standards is there, and it is possible to solve this problem in 2021.
To put it simply, participants in this process will have to develop product standards that lay down the norms and requirements for reinforced polymer pipeline systems. Another group of documents would cover process standards: the design, construction and operation of facilities using reinforced polymer pipes. Each different Technical Committee (TC) at Rosstandart is responsible for different areas of standard-setting. TC 241 is responsible for supporting the development of standards for polymer pipes, fittings, other plastic products and test methods, while TC 23 is responsible for equipment and technologies used in oil and gas production and processing. Its mandate extends to standards for the design, construction and installation of equipment in hydrocarbon production. According to the minutes of the Government meeting, the participants of the interdepartmental working group, as well as manufacturers and consumers, should coordinate their efforts and harmonise the process of preparing standards and putting them through the approval procedure.
What is the size of this market? Who are the key players, and will foreign producers who have a track record with oil and gas companies displace domestic producers?
MK:
The bulk of the pipelines we are talking about are owned by four oil companies: LUKOIL, Rosneft, Surgutneftegas and Gazprom Neft. Their combined pipeline network length measures 189 thousand km. If we take global estimates as a basis, the potential market for polymer pipes is 40%–45%, or 80–85 thousand km. There is an interest for Russian products in the oil-producing countries of the CIS: our Group has made shipments to Ukraine, the Baltic states, Uzbekistan, and the Caspian countries.
In addition to us, there are three or four other manufacturers on the domestic polymer pipe market. We rarely compete, as we often do business in different segments. As part of our work on standards, we act together, representing the interests of the industry in a unified manner.
Foreign companies are showing interest in the Russian market. Manufacturers fr om the United States and Europe have tried to enter it, and several Chinese copies of foreign pipes have appeared.
The shop at POLYPLASTIC Group’s Klimovsky plant.
Oil and gas companies in North and South America and the Middle East have been using polymer pipes for decades – their share in the total volume reaches 40%
By developing a regulatory framework, are you not opening up the market to foreign competition?
SS:
At the outset, yes, this is possible. When there is no domestic manufacturer, a foreign one will quickly appear. But the situation here is different. Let’s not get into other companies, but our Group has invested hundreds of thousands of dollars in R&D, production facilities, and training. Our products have repeatedly been approved against technical specifications, and we have introduced our own polymer systems at oil and gas facilities. It is obvious that in the absence of regulation, the operational requirements for products were more stringent than is currently laid down in the standards. Our technology now works effectively, and our products are used by employees at LUKOIL’s facilities in Kaliningrad, the Volgograd Region, the Stavropol and Perm Territories. They have also been tested in the Tomsk Region. Several projects have been implemented with Bashneft, TATNEFT, and a number of regional players. Negotiations on the use of polymer systems in the northern oil producing areas are ongoing. We have been manufacturing products for other sectors of the economy for several years now: we know how to scale our business and will definitely compete with our foreign peers for the domestic market. Moreover, we have a number of advantages over the competition: stable and predictable supplies of raw materials, barrier-free cross-border operations, our owned production facilities, beneficial state policy promoting import substitution and the construction of production facilities for deeper conversion of hydrocarbons, export support, and many more. We have a good chance of winning this fight.
How is polymer pipe production technology developing? What research is being conducted, what are the producers of raw materials and final products aiming at?
If we take global estimates as a basis, the potential market for polymer pipes is 40%–45%, or 80–85 thousand km. There is an interest for Russian products in the oil-producing countries of the CIS, the Baltic states, Uzbekistan, and the Caspian countries
MK:
R&D is needed to develop a new market, create products and adapt them to customer demands. We are actively investing in our laboratory facilities, which are already among the best for polymer pipe testing in Russia. Coming back to the question of whether reinforced polymer pipes can be operated at a pressure of 210 atmospheres, equipment is needed for testing that can create a pressure of 400–500 atmospheres or more. And this applies to every parameter. To adapt the pipe to chemically aggressive environments, tests are carried out with different types of polymers, and the impact of different environments on their working surfaces is observed. Pipeline systems don’t just consist of pipes, but also have various connections, taps, wells and other technical products. Their design, creation, testing, pilot operation, certification, and production are an important part of R&D.
SS:
The key areas of research, in addition to boosting the maximum pressure, are the search for materials and methods for reinforcing polymer pipes, increasing their temperature stability, reducing gas permeability, and increasing resistance to corrosion. Another important area is the use of thermal insulation to reduce heat loss during oil transportation. The lower the temperature, the higher the viscosity of the raw material, meaning it is more difficult and more expensive to transport. The polymer industry is developing at a very fast pace. As new grades of polymers enter the market and are used more, manufacturers regularly introduce products with new properties. We are confident that the oil and gas industry is just the latest market wh ere polymers can up-end business economics, displace legacy technologies and make production safer and more efficient.
Download PDF
Maxim Kovyazin
CEO of POLYMERTEPLO Group (part of POLYPLASTIC Group)