At the end of 2020, a webinar dedicated to SBS polymers in the adhesives industry took place on the SIBUR Business Practices platform. The participants of this online client meeting discussed global trends affecting the production and consumption of this type of chemical product, evaluated SIBUR’s product offerings, and shared their own views and ideas about the outlook for the segment.
In his welcoming address, Alexander Petrov, Member of the Management Board at SIBUR, stressed that despite the strong economic headwinds over the past year, a milestone event took place on the Russian market: at the Company’s Voronezh site, a plant with the capacity to produce an additional 50 thousand tonnes of thermoplastic elastomers (TPE) was launched. As part of the launch, SIBUR brought seven new grades to market, some of which are targeting adhesives manufacturers. Our Elastomers R&D Centre, which now features an adhesives laboratory established as part of the launch of production facilities, is focused not only on supporting production, but also on working to fulfil individual orders of customers in the adhesives segment.
A total of 80% of the consumption of adhesives and sealants is driven by three industries: boxing and packaging, construction and the automotive industry
“SIBUR today not only, as previously stated, ‘supports the sales of its products’, but also attentively listens to how the customer does business, what values are important to them, and looks for opportunities for cooperation in the interests of both parties,” Alexander Petrov stressed.
Changes in the industry
In her presentation, Ekaterina Krasnova, Executive Director of the Association of Sealants and Adhesives Manufacturers, highlighted several key areas where the industry is changing. She explained that while scientists fr om the twentieth century first created formulations, and then began to search for niches wh ere they could be used, in the twenty-first century, the situation has been flipped on its head. Nowadays, production and science first determine the necessary properties of materials, after which work on their formulation begins. Therefore, the key industry trends follow the needs of customers.
First trend: ergonomics. The consumer needs light and reliable materials. Plastics have overtaken metals; bonding or gluing have overtaken welding. These processes are central to the electronics and automotive industries, where the use of polyurethane adhesives and hybrid polymers is constantly growing.
Second trend: energy efficiency. Building materials must keep up with the demand for increasingly higher efficiency. The answer is to expand the use of silicone sealants, adhesives, and hot melts, which are displacing old formulations and traditional building materials.
Third trend: environmental friendliness. Requirements to reduce the use of volatile organic compounds (VOCs) and cut CO2 emissions have led to an increase in demand for water-based or solvent-free adhesives, which are based on polyurethanes or renewable plant and animal materials.
Of the seven new TPE grades introduced by SIBUR in 2020, three – SBS L 7322, 7417 and 7420 – were formulated to directly meet the demands of domestic manufacturers of furniture adhesives, adhesive tapes and hot-melt adhesives
Fourth trend: safety. Despite the fact that this trend encompasses many different aspects, fire safety is particularly relevant for today’s adhesives industry, as consumers look for low-flammable or inflammable materials
Fifth trend: versatility. At production facilities, adhesives are required to be easy to manufacture and handle. Ideally, one adhesive or one group of adhesives should work across different technological sites.
According to Ekaterina Krasnova, in the field of R&D (both in Russia and globally), the main areas of focus today are the use of composite materials, the creation of formulations focused on extreme operating conditions (cryogenic or ultra-high temperatures), fire-resistance, and minimising the use of VOCs and other toxic substances.
Krasnova also gave an overview of the global market in her presentation. She explained that 80% of the consumption of adhesives and sealants is driven by three industries: boxing and packaging, construction and the automotive industry.
The most dynamically growing adhesives and sealants markets include: South-East Asia (India, Vietnam, China, South Korea, Taiwan and Singapore) and Europe (Russia, Hungary and Poland).
The major consuming regions: Europe (35%), South-East Asia (33.4%), North America (25.5%). Russia accounts for 10% (2019, 0.53 million tonnes).
Stable markets see growth of +2%–4%, while emerging markets post +5%–7%. With this said, experts fr om the magazine Adhesives & Sealants Industry estimated the global market for these products at USD 38.9 billion in 2018, meaning that by 2022 it should reach USD 53.5 billion, and USD 98.57 billion by 2027.
In March 2020, the GOST “Sealing and curing polymeric building materials. General technical conditions” came into effect. The text of the standard was written by experts fr om the Association of Sealants and Adhesives Manufacturers.
Elina Shevchenko, Senior Marketing Expert for SBS polymers at SIBUR, followed on with the theme of trends by explaining the situation with the SBS market in the adhesives industry in her presentation. According to her, global consumption of SBS polymers sits at 1.8 million tonnes, growing at +3% annually. However, this trend was “broken” by COVID. Over 2020, consumption had actually dropped to 1.5 million tonnes.
The lion’s share of SBS is produced in Asia (64%), while the Americas produce 14%, Europe 15%, and Russia 6%. Consumption broadly shadows production: Asia consumes 56%, the Americas 22%, Europe 18%, and Russia 3%.
The main consuming industries of SBS polymers are road construction (30%), roofing (25%), compounds (26%) and adhesives (20%).
The top three sub-segments in the adhesives industry wh ere SBS polymers are used are hygiene products (< 1 mtpa of adhesive, +4% CAGR), packaging (~4 mtpa, +3% CAGR) and transport (1 mtpa, +10% CAGR). Each of these segments has its own growth vectors that affect the volume of adhesive consumption.
Nowadays, production and science first determine the full range of properties of materials, including their consumer properties, after which work on their formulation begins. Therefore, the key industry trends follow the needs of customers
Hygiene products. On the one hand, there is growing demand for superabsorbent materials used to make diapers, which increases the demand for SBS polymers. On the other hand, manufacturers are trying to reduce the production costs of hygiene products, including by optimising their design. For example, the thickness of the adhesive layer is reduced wherever possible without having to compromise on quality. This means that there are two opposing trends that are keeping a balance in the consumption of SBS polymers. A third trend, which is still only in its infancy but may impact the industry in the future, is the use of alternative bonding technologies (ultrasonic bonding and infrared bonding). These methods are already being used experimentally, but we are yet to hear any talk of mass production using these technologies.
Packaging. On the back of the explosion in online commerce (which was only further bolstered by the pandemic), the production and consumption of packaging continue to grow. This has a positive knock-on effect on the consumption of adhesives used in the production of packaging. Meanwhile, there is a strong demand for environmental friendliness in Europe. Manufacturers are actively ditching mortar adhesives, replacing them with hot-melt adhesives, and developing technologies for the production of water-based adhesives. Another manifestation of this trend is monopackaging. This is the idea of cutting down on the use of a large number of different materials, including adhesives, sometimes going as far as completely rejecting them, in order to make recycling of packaging materials as simple as possible. Monopackaging has not yet come to the mass market, but the idea is actively discussed.
Heat-conducting adhesives are widely used in the production of electric vehicles.
The automotive industry. The European requirement to reduce the weight of cars is forcing manufacturers to use more structural adhesives instead of soldering and riveting parts, a swap that significantly increases the consumption of adhesives. The growth in the production of electric vehicles also entails the widespread use of heat-conducting adhesives. The requirements for car interiors are constantly being tightened up, which pushes manufacturers to use new materials, including sealants and adhesives. For example, nowadays, even the level and composition of the new car smell itself are regulated!
The main areas that R&D focuses on today are the use of composite materials, the creation of formulations focused on extreme operating conditions (cryogenic or ultra-high temperatures), fire-resistance, and minimising the use of VOCs and other toxic substances
The latest solutions
Vyacheslav Evtushenko, SBS Technical Service Manager, spoke about SIBUR’s product range during the event. He explained that the development of SIBUR’s Voronezh site, the elastomer production hub within the Company, is taking place in stages. Although with its new additions in previous years the Company primarily focused on the production of TPE to meet the demand for standard grades for the construction industry, this latest launch in 2020 is focused mostly on expanding the grade mix for all applications, and primarily for specialised segments. Of the seven new TPE grades introduced by SIBUR in 2020, three – SBS L 7322, 7417 and 7420 – were formulated to directly meet the demands of domestic manufacturers of furniture adhesives, adhesive tapes and hot-melt adhesives. The new molecular design used in these grades of adhesives will unlock formulations for a range of applications, and will compete with comparable foreign grades both in terms of price and physico-chemical properties. Vyacheslav Evtushenko spoke separately on the properties of new grades and the outcomes of research into formulations of adhesives, which was conducted at the Company’s R&D Centre in Voronezh. In addition, he announced that the development of a new grade of adhesive had been launched: SBS L 7317 is needed for self-adhesive roofs and sealants, but it may also be interesting for those in the traditional adhesives market. This grade is already slated for market launch in 2021.
Next to pick up the baton was Svetlana Kotova, PhD in Chemistry at the F.F. Koshelev Department of Chemistry and Elastomer Processing Technology, Lomonosov Institute of Fine Chemical Technologies, RTU MIREA.
She presented formulations of adhesives for the furniture industry and adhesive tapes, created using the new grades of adhesive SBS polymers produced by SIBUR. She shared the findings of the analysis of their characteristics, noting their solid consumer properties vs foreign competitors, and spoke about the formulation and technological methods used to modify the properties of SBS adhesives.
Dr Walter Ramirez, Founder and Chief Innovation Officer at Innventik S.L., continued in the same vein, speaking about the properties and applications of SBS polymers in the adhesives industry. He elaborated on the molecular structure of SBS polymers, the methods used to modify their properties, and the effect they have on the final product. He also went into detail on the benefits of SBS as a polymer base for adhesives over other polymers, as well as the possibility of replacing styrene-isoprene-styrene (SIS) polymers in PSAs for packaging tapes and adhesives for hygiene products. In the concluding remarks of his presentation, Dr Ramirez said, “SBS polymers allow for a more efficient management of energy consumption and cost of the final adhesive, simply because SBS-based adhesives have better processability and can contain the optimal ratio of polymer and adhesive agent.”
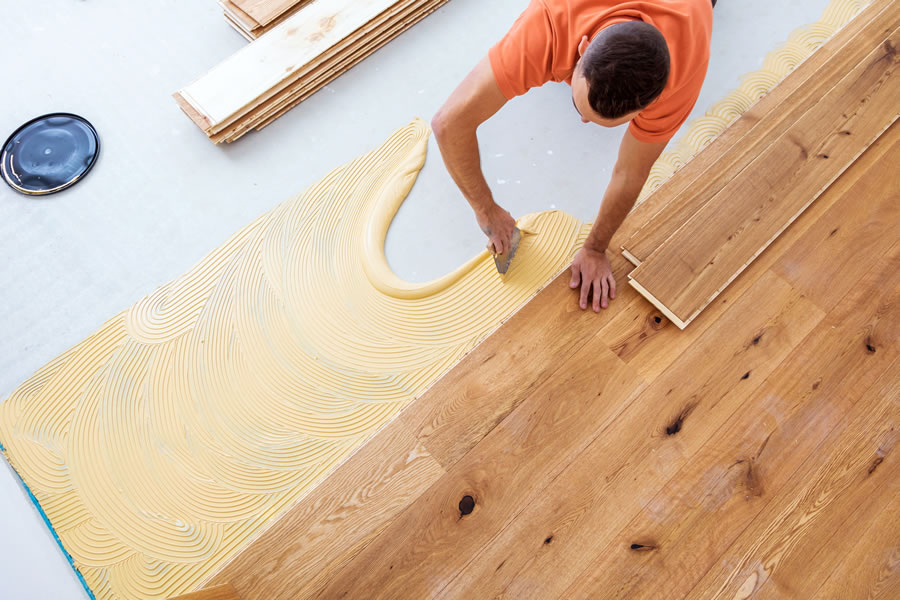
The consumption of DIY adhesives has shot up during the pandemic, with people deciding to carry out repairs during lockdown.
Environmental trends and the impact of the pandemic
At the end of the client webinar, the participants were split into groups on two topics, “Environmental trends in the adhesives industry” and “The impact of the pandemic on the adhesives industry”, where they shared their own takes on the situation and exchanged views on emerging industry trends. The first to give their thoughts about the webinar was Timofey Kalinin (from Egida+), who identified a relevant trend for adhesives manufacturers: “Our team produces adhesives for mattresses and upholstered furniture. The trends towards eco-friendliness and the circular economy are relevant to us as participants in the global market. Today, we are faced with a large number of problems around how materials are recycled. Since the different layers of our customers’ products are glued together, it is vital for us, from an environmental point of view, to develop types of adhesives that are reliable and durable during operation, but that can also be easily separated from the other materials during recycling.”
There is a strong demand for environmental friendliness in Europe. Manufacturers are actively ditching mortar adhesives, replacing them with hot-melt adhesives
In his response to the comment, Vyacheslav Evtushenko noted that this kind of task was formidable and ambitious, thanked the participants of the webinar for raising it, and promised that SIBUR’s specialists would get to work on a solution for it.
Ilya Lapochkin, (from Egida+), raised the impact of the pandemic on adhesives manufacturers. He said that on the one hand, there was a reduction in sales volumes (although marginal). In response, companies moved to actively diversify their product portfolios. In particular, the supply of polyurethane adhesives, hot-melt adhesives and others is on the rise.
“The pandemic has had a very uneven impact on the industry. We have all ordered a lot of things online, meaning the demand for packaging and adhesives in this segment has grown significantly. The same applies to food and hygiene products: people did not lim it their consumption in these segments, quite the opposite,” said Elina Shevchenko. “Interestingly, the consumption of adhesives for the DIY segment rose during lockdown: confined to their homes, people decided to make some small repairs. The situation was completely different for light industry and the automotive industry. These industries took a huge hit from the pandemic, which had a knock-on effect on the volume of adhesives sold.”
Download PDF