Christoph Roehrig, Head of BASF in Russia and CIS, noted that, “the partnership between BASF and SIBUR is developing at a fast pace, despite the difficulties caused by the pandemic, and the leading petrochemical companies are facing similar challenges”. He spoke about how and why it is essential to introduce principles of sustainable development into every aspect of activity, on what industries BASF’s innovative efforts are focused, and what is the foundation for the company’s further successes.
How is collaboration between BASF and SIBUR developing?
I believe that the relationship between BASF and SIBUR has become a model partnership on the Russian market. We have been working on strengthening ties since 2016. It was back then that it became clear our collaboration would be prosperous and we’ll have more and more projects together. This led to the idea to create a coordination committee and to have the leaders of both companies meet regularly. At least once a year we hold this event at the highest level where I, as the Head of BASF in Russia and CIS, represent our company, and Sergey Komyshan, Managing Director and Head of Basic Polymers Division, acts on behalf of SIBUR. We do not only discuss current operational topics, but also future strategy: how our businesses are developing and how they must evolve in order to respond to the upcoming challenges. We share our best practices and learn from each other.
A prime example of collaboration is our joint project at SIBUR PolyLab to develop innovative solutions in the production of polymers
A prime example of our collaboration is our joint research effort at SIBUR PolyLab at Skolkovo for developing innovative solutions in the production of polymers. At the centre, we are focused on creating modern and environmentally friendly synthetic materials which can then be recycled. The efforts from both companies are undoubtedly significantly contributing to the development of polymer recycling in Russia.
How has the pandemic affected your partnership?
Without a doubt, 2020 has impacted the agendas of both our companies. We have shifted more communication online, but have not let this prevent us from continuing our series of workshops on the SIBUR Business Practices platform, originally planned to be held offline at the Skolkovo PolyLab. As a result, seven trilateral webinars were held last year. They were attended by more than 300 specialists and experts from BASF, SIBUR, and its clients.
Unfortunately, due to the pandemic, a number of projects scheduled for the first half of 2020 had to be postponed. For example, in December of last year, BASF and SIBUR signed a memorandum of understanding formalising their partnership on the sustainable development and circular economy agenda, and as a first step, a workshop was supposed to take place at BASF headquarters in Ludwigshafen, Germany. Unfortunately, due to lockdown measures and the suspension of international flights, this could not happen. However, any situation can be turned into an advantage, and shortly thereafter, the workshop was held online and in an extended format. Around 100 people took part in the event, not only from our head offices, but also from units all across the world. Gathering everyone in a conference hall in a usual format would require significant effort, not to mention considerable expenses, as it would be necessary to coordinate the schedules of all participants, and also organise travel, accommodation and meals.
Since 1992, BASF has been following the international Responsible Care programme, which ensures the safe handling of chemical products during their entire life cycle. In 1994, the chemicals giant declared its commitment to sustainable development, and in 2011 formulated its goal “We create chemistry for a sustainable future”. What steps have been taken since then, and what difficulties have been encountered?
Sustainable development is an extremely important topic for us. Look around you! Our products are not only used to develop high-tech materials for the oil and gas, aerospace, construction and other industries, but they are also used in the production of almost everything that surrounds us in everyday life. For example, cars and public transport, materials for decoration and thermal insulation, footwear, cosmetics, and food both directly due to vitamins and other food additives, and indirectly due to crop protection products. Both BASF and SIBUR are major chemical companies, so we attract a lot of public attention. We have simply got to be at the forefront of implementing strategies for sustainable development. Our company has already identified a number of products which we will soon stop producing, since they are no longer fitting our increasingly tough requirements for sustainable development. SIBUR is doing the same. This is a competitive edge that we share. Sooner or later, every company will have to face questions of sustainable development.
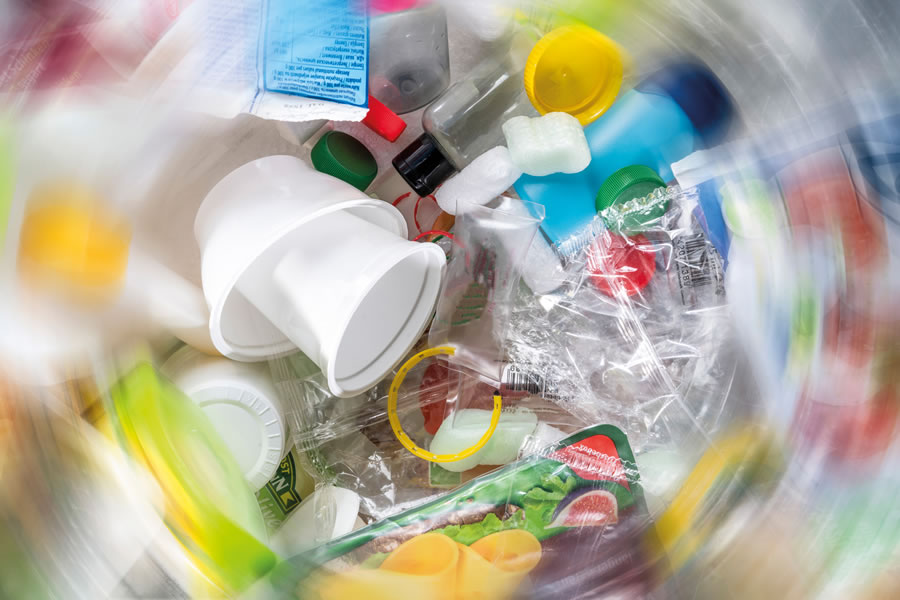
Separating household waste is an important step towards a circular economy.
BASF has long been a part of an active public discussion about what the contribution of companies to environmental protection should be, initiated in Western Europe as far back as 25–30 years ago. We have already come a long way, and on 26 March of this year, BASF published an ambitious roadmap plan to achieve net zero emissions by 2050. The plan is to reduce greenhouse gas emissions by 25% by as early as 2030, despite the imminent launch of a large production facility in China. In total, we will reduce our emissions by approximately 60% compared to 1990 levels, which is even higher than the EU target of 55%. Of course, this will require a serious investment of around 3–4 billion euros.
2020 had an impact on our agenda. We have shifted to online, but did not stop our workshops on the SIBUR Business Practices platform, already attended by over 300 experts from BASF, SIBUR, and its clients
There is still a lot to be done in Russia. But the examples of SIBUR, LUKOIL, Gazprom, and Rosneft show that the effort of Russian petrochemical businesses is moving in the right direction. One of the main difficulties is that for the implementation of significant projects in a circular economy, the goodwill of companies is not enough, an infrastructure needs to be built. I will explain using a simple example: to establish recycling, a reliable supply of raw materials is a must. Meanwhile, in Russia, even the simplest sorting of waste in households is still not very widespread. You have probably heard that in German homes there are four bins for different types of waste? At the same time, it is not enough to just separate the waste, it must also be properly prepared: residues in the packaging can affect the recycling and result in a product with different properties than planned. Therefore, companies need to engage in a dialogue with society, raise awareness amongst people, and gain their support.
A dialogue with government authorities is also vital. It should be noted that significant progress has been made on issues related to sustainable development in legislation. For example, at the end of 2020 and beginning of this year, Russia’s President and Government took a set of measures aimed at implementing the state science and technology policy towards green development and the significant reduction of greenhouse gas emissions. This is encouraging large companies to introduce decarbonisation programmes.
However, at the same time, there is a lack of precise legal definitions for mechanical and chemical recycling and, consequently, a lack of legislation that would stimulate companies to use recycled plastic for industrial purposes, and this is a serious obstacle in many countries to the expansion of our ChemCycling project. The main idea behind this initiative, launched in 2018 in Ludwigshafen, Germany, is that our partners recycle plastic waste into pyrolysis oil (we call it chemoil), which the BASF industrial complex (Verbund) then uses as an alternative to fossil resources, like oil or gas.
For the past three years, the BASF plant in Ludwigshafen, Germany, has been using pyrolysis oil derived from recycled plastic as an alternative to fossil fuels. Photo: BASF
Last year, the first commercial products from recycled materials processed under the ChemCycling programme were released to the German market: packaging for mozzarella, components for refrigerators, etc. How soon will products from recycled plastic appear on the Russian market?
It is a complicated task for all countries, including Russia. Manufacturers of recycled packaging and its consumers are facing universal difficulties with the implementation: the need to create infrastructure, and insufficient legislative framework. But we are confident that not only global, but also local manufactures will start to use recycled plastic to create packaging. From our side, we offer on the Russian market a range of solutions that make mechanical recycling of plastics easier: for example, Irganox® 1520 L, a liquid antioxidant for rubber; Irgatec® CR 76 IC, a modifier for non-woven polymer (among other things, meltblown for the filter layer in medical masks can be produced with it), and products under the Chemetall brand for washing PET or HDPE, and many others. Our KPIs for sustainable development apply to the entire geography of BASF’s business: we aim to achieve the same standards in all our regions.
ON 26 MARCH OF THIS YEAR, BASF PUBLISHED AN AMBITIOUS ROADMAP TO ACHIEVE NET ZERO EMISSIONS BY 2050
Recently, the number of BASF industrial sites in Russia has changed. Why is this?
Last September, we sold our global Construction Chemicals business to Lone Star. It includes facilities in more than 60 countries. As a result of the transaction, the Russian production sites in St Petersburg, Podolsk, Krasnodar and Kazan changed ownership. It should be noted that if BASF had kept this business, the number of local sites would have increased. We were working on opening a production facility in Pavlovsky Posad, on a territory adjacent to the existing BASF automotive paints and coatings plant.
The Russian Government is encouraging import substitution, and so we are continuing to search for the right partners in the implementation of local projects. Additionally, we are continuing to develop existing local projects.
Back in the 1990s, BASF, together with a Russian partner, started producing crop protection solutions in Volgograd. We had a long and fruitful cooperation, but unfortunately, it ended due to circumstances beyond our or our partner’s control. We found another counterpart in Kirovo-Chepetsk, and in the past years our volumes tripled.
One more example: in 2019, together with a partner, we launched the production of surfactants in Dzerzhinsk, which serve as a feedstock for manufacturing cosmetics and household chemicals.
In 2020, we helped to arrange local production of plasma-coated canisters, which were previously purchased in Europe. This significantly reduced delivery time and carbon footprint from their transportation.
BASF supplies farmers not only with crop protection products, but also with seed material and digital solutions.
Tell us about new BASF products. What future projects are currently being developed at BASF?
The last century was a time of exciting scientific breakthroughs, with science making huge leaps forward with each new discovery. Now a push for sustainable development has become the key driver. The automotive industry is undergoing some of the most revolutionary changes. BASF materials are currently being used in the production of almost every car part, from plastic interiors and components to fuel additives or brake fluid. Materials for electric vehicles and automated driving are areas that we actively invest in and strive to become a major supplier (for example, BASF recently launched Ultradur RX material that protects sensitive electronics from disturbing electromagnetic waves from other vehicles; also, the company is actively involved in the production of battery materials for electric vehicle industry. Ed. note).
Another example of an eco-friendly innovation is the startup trinamiX, founded by BASF. Its specialists have created equipment allowing you to sort plastic waste in a matter of moments
Another innovative industry is agriculture. BASF has already become a major player in the market for crop protection and animal nutrition additives. But nowadays in this industry you need to not only offer crop protection products, but also supply farmers with seeds and even provide digital technologies. BASF is actively advancing in this area. For example, in July 2020, BASF acquired Cloudfarms, a developer of software for managing livestock farms, and we also offer industry-specific applications and programmes: for example, Scouting allows you to identify diseases and weeds from photos, and Field Manager creates three-dimensional models of fields and gives recommendations on how to manage them.
It should be noted that in all spheres and all markets that we are active, we are constantly working on improving our products, and our branches are, first and foremost, research centres. Our experts are focused primarily on the development of new processes with lower CO2 emissions. The technology for emission-free production of hydrogen from natural gas should be noted as one that will result in getting as a by-product safe and in-demand granular coal instead of CO2. Another promising growth area for BASF is the creation of methods for the emission-free production of olefins, the main intermediate in the chemical industry. We are testing an eco-friendly way of their production based on methane, not naphtha.
As part of its decarbonisation programme, or Carbon Management programme, BASF is making significant efforts to reduce greenhouse gas emissions during all stages of production and plans to increase the share of renewable energy sources in its consumption. At the moment BASF is working on the realization of a pilot furnace for the world’s first electrically heated steam cracker, which will reduce carbon emissions by 90%.
Another example of an eco-friendly innovation that clearly demonstrates the benefits of digital technology in the chemical industry is the startup trinamiX, founded by BASF. Its specialists have created equipment just a little bigger in size than a smartphone allowing you to recognise and sort various plastic waste in a matter of moments, using a portable sensor and a mobile application with cloud technology. All of these innovations are of interest to SIBUR, and I think that thanks to them we will identify new areas to strengthen our partnership.
The trinamiX portable spectrometer and mobile app allow plastics to be precisely detected and sorted. Photo: trinamiX.
In December 2020, BASF signed an agreement with Voronezh State University (VSU). What results does the company expect from this partnership?
We have talked a lot about BASF’s products, but we must not forget about a key factor contributing to the company’s success. Our people. You may well have the most innovative products, but if you do not have a strong team, you will rapidly fall behind competition. Russian universities are full of smart and passionate people. Thanks to them we can be successful not only now, but also in ten, twenty, fifty years. Universities are exactly the place where people are creating things which can change the future. This is why the main task in the partnership with VSU is to engage the university’s strong scientific community on BASF’s R&D programmes and build a talent pipeline for our company.
Our commitment to helping our customers build a successful business is the main task that all BASF employees can and should work on
We have also signed a partnership agreement with Voronezh State Agrarian University (VSAU). Through this partnership, our company’s agricultural solutions and technologies will be studied and evaluated at a local level, as well as through practical research. BASF has many crop protection products that have proven to be highly effective in different parts of the world, but they will be performing best for Russian farmers if they are adapted to local conditions: climate, soils, precipitation, etc.
These efforts began in the mid-2000s, when BASF founded an agricultural centre in the Belgorod Region. Essentially, we cultivated a large field using different technologies on different parts of it. It has become not only a great testing ground for us, but also an amazing marketing tool. Farmers came to us to see the differences first hand: over here, the crop is treated using standard methods, and over there with the help of BASF technologies.
What are BASF’s plans for the nearest future?
One of the main challenges facing BASF now is demography. I may feel like I’m 25, but unfortunately, I’m actually about to turn 60. And there are a lot of people of my age in the company. I think that in the next four to five years, quite a few of our colleagues will be retiring, and this means that we need to prepare successors. In Russia, like all around the globe, it is extremely important to identify potential leaders, provide them with opportunities for growth, training and development, as well as to recruit new members to the team by attracting the best candidates entering the labour market.
The company has the same leadership standards and one code of conduct everywhere, it also ensures equal opportunities for job seekers in any country and welcomes employees moving abroad. To achieve our global target of 30% women in leadership positions by 2030, we are running special programmes where women are able to speak with our mentors and external coaches. For well-being of our whole team, we create an environment that helps employees to maintain a healthy work and life balance: we offer the opportunity to work remotely, we are willing to deliver necessary equipment, and provide high-quality medical insurance and social packages.
As the second point, I’d like to mention that the world is becoming ever more digitalised. In BASF, many projects are focused on developing and implementing new digital tools in all areas. Of course, this also applies to sales. In April of last year, BASF opened its first online store in Russia, selling crop protection products.
Third and foremost, we must continue to prove that customers are important to us, and that the ultimate goal of all the processes in our company is to meet their needs as fully as possible. Helping our customers to become better in their enterprises remains therefore the most important topic where all employees of BASF can and should contribute to. If our customers are successful with our products, we have a high chance to become their preferred partner, which makes us as well successful. This is the way we contribute to a world that provides a viable future with enhanced quality of life for everyone.
Download PDF