DPO Plastik started operating in 1965, more than half a century ago. What helped you to stay afloat during all the economic and political crises?
Being a multifaceted enterprise gives us an advantage. Our plant has six polymer processing facilities operating independently from each other. These include packaging, industrial goods and composites. We manufacture products for a variety of industries, including food, automotive, railway transport and healthcare industries, and also government defence procurement.
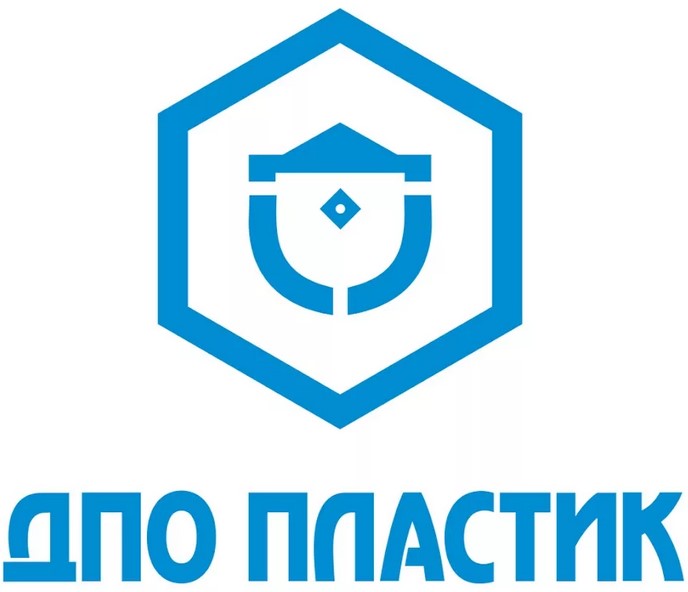
DPO Plastik is a manufacturer of polymer packaging and industrial goods. For 50 years, the company has been supplying various businesses while keeping pace with the market, and has nearly 1,000 employees engaged in production.
In crises, some of our production areas were down, while others continued driving the entire business. For example, a decline in the automotive industry was offset by government defence contracts. We allocated resources to areas where we saw potential, making sure we stayed busy and kept pushing forward the entire Russian industry.
Another advantage is our team. Dzerzhinsk is a small town, where our plant employs families and even generations. Our employees stick up for each other and are a close-knit committed team of people who share the same values, making our company run like a well-oiled machine for years.
They are the driving force behind a lot of positive transformations, new products launched to the market, new formulations and the company's efforts in a variety of promising areas. Our team applies advanced domestic and international solutions to improve its management and production processes.
For example, it was the team’s initiative that helped DPO Plastik introduce a mushroom tray box for champignons in 2017. Two years ago, it was a real innovation for the Russian market that outperformed all other manufacturers in terms of production costs. With a weight of just 150–180 g and an 8-second production cycle, the tray box then had the smallest weight and was the quickest to make. Also, we were the first Russian company to fill this niche.
What products do you manufacture for automotive, healthcare and food industries?
PVC is our flagship production. We make PVC for food products, healthcare and construction. This includes confectionery, syringes and suppositories packaging, along with window sill films and wall panels. We have expertise in making multi-layer barrier films for food packaging, including films with printing.
Cast barrier film production line.
Various types of containers make up a significant part of our production. We also manufacture what we call “car packaging”: bumpers, fenders, interior and exterior parts, and other solutions for cars. Quite a large segment for us is production of composite-based products, including pipes for grenade launchers and missiles using filament winding technology.
Our plant has six polymer processing facilities operating independently from each other.
The company is implementing an innovative project to develop and manufacture type 4 polymer-composite gas cylinders for vehicles and filling stations. What are its outstanding features?
With our 50-year presence in the composite materials market, we have a strong track record of making composites using winding technology, which include type 4 gas cylinders. They are fully polymeric, with even liners made of polyethylene, in contrast to type 1, 2 and 3 gas cylinders, which have metal liners. The liners are wrapped in carbon fibres and glass fibres. This technology is unprecedented for Russia.
Its main advantages are the light weight of the cylinders, no corrosion, fire safety and warranty period twice as long as that of other gas cylinders types. Also, with lower mass, the vehicle consumes less fuel, which increases the service life of its chassis. Russian automakers AvtoVAZ, KAMAZ and GAZ have all expressed their interest in developing this new technology.
KIRION (blow moulding machine).
PVC is our flagship production. We make PVC for food products, healthcare and construction.
We are also planning to produce large gas cylinders for mobile fuel stations. With a capacity of 320 litres, they will be three times bigger than the standard vehicle gas cylinder. One station contains 50–60 tanks and is used for refuelling in hard-to-reach locations, e.g. in the Far North. This project is being discussed with Gazprom, among other partners.
Having invested quite a lot of effort in this area, we are almost there: we have chosen the production site and carried out all the R&D required. Facilities construction is nearing completion, and we are expecting to have the equipment delivered very soon now. The launch of production is planned for the end of 2019.
Why are you so optimistic about this endeavour?
The use of natural gas is a major trend for the world’s automotive industry. Compressed natural gas is a motor fuel that is second to none in terms of economic, environmental, resource and technical parameters.
Fisher & Krecke (flexographic printer).
No furniture films production has been launched in Russia yet, so we believe we will be able to take up a major part of this segment.
We can see CNG gaining popularity, as evidenced by practices of global car majors. Almost all European automakers produce flexible-fuel vehicles. Experts predict a 10-fold increase in natural gas vehicle sales by 2022.
The global composite materials market is growing by more than 20% annually, while in Russia, this indicator accounts for less than 1% of the world’s ratio. The Russian composites market has only reached RUB 50 bn, compared to ca. USD 700 bn of the global market. There is room for improvement here. Gas cylinders are the technology of the future.
What are the company’s priorities for 2019?
Launching the production of type 4 gas cylinders is our main priority, but we have other plans for 2019 as well. Our second biggest project is also about the automotive industry – it is large injection moulding. We are currently acquiring new equipment and engaging additional resources in this area. Instead of maintaining a single focus, we aim to develop a holistic manufacturing hub capable of addressing the latest challenges. Goods manufactured with the use of different technologies (e.g. extrusion, forming and different composite solutions) are popular in the market.
ENGEL duo 3200 (injection moulding machine for large parts).
Petrochemical sector is currently at the heart of Russia's industrial scene.
We are also considering the idea of launching production of PVC films for doors and furniture. Although we have an extensive experience with PVC coatings, this project will require a slightly different type of equipment. No furniture films production has been launched in Russia yet, so we believe we will be able to take up a major part of this segment.
How much do you rely on using domestic feedstock and materials for production purposes?
Currently around 70% of the feedstock we use is sourced from Russia and we are planning to increase this figure. We are therefore looking forward to the launch of ZapSibNeftekhim which will manufacture the items that our сompany has to buy abroad.
JSW J280ADS (injection moulding machine).
What are the key areas of cooperation between your company and SIBUR?
DPO Plastik and SIBUR have a long track record of cooperation. We purchase from SIBUR ca. 1,000 tons of suspension resin used in PVC films production on a monthly basis. Our cooperation covers the supplies of polyethylene and polypropylene used in flexible packaging materials.
We really appreciate working with SIBUR, as it offers excellent support and is always quick in providing feedback. Any and all issues are solved as soon as they arise. Any meeting with SIBUR is more about focusing on new opportunities rather than overcoming bottlenecks, as there are none. So SIBUR builds strong relations with partners.
KAMPF (cutter).
What do you think about evolution of the petrochemical industry over the past few years?
Petrochemical sector is currently at the heart of Russia's industrial scene. It has a far-reaching macroeconomic effect on economic growth.
Winder.
There have been significant improvements in this area, such as enhanced feedstock quality and a wider range of new domestic products. Though some segments remain import-dependent, the outlook is positive. SIBUR takes active part in making this transformation happen. And we hope that the launch of ZapSibNeftekhim will enable us to make a breakthrough in terms of both feedstock quality and market predictability.
Petrochemical industry has a high upside potential. The main thing here is not only to keep up with the industry trends but to become a trend-setter.
Download PDF