Polymer dispersions are among the Company’s key products. What are the specifics of their production in Russia? How often do you need to take an individual approach to your customers?
We have been in business for some 20 years now, having mastered a variety of technologies used in the manufacturing of polymer dispersions. Among our strengths is that our product properties are formed directly in the process of organic synthesis.
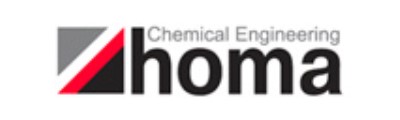
HOMA has been operating since 1998, focusing on the development and production of polymer dispersions and adhesive materials for multiple industries. By 2017, HOMA’s total production capacity was over 30 ktpa.
In addition, we are Russia’s only manufacturer of water-based polymer dispersions that provides full-cycle support – fr om developing materials to delivering them right to the customer's production line. Our R&D centre verifies the quality of the products made of our intermediates.
Strict quality control and careful consideration of customer requests provide for continued popularity of our products in the market. Thanks to the continuous interaction with our customers and their feedback we are able to develop innovative products, launch new production lines, and tap into market segments that are beyond the reach of our peers. For example, we have developed adhesives with permanent stickiness used in the manufacturing of masking tape, stickers, and labels, marketed a new plasticiser for mortar mixes, and tapped into the paper & pulp industry, wh ere water-based polymer dispersions are in high demand. Among our major customers is Goznak, Russia’s banknote manufacturer.
What is your product development strategy for the upcoming years?
We have ramped up production of styrene-acrylic dispersions and expect to complete the expansion and upgrade of the vinyl acetate dispersions line by March this year.
Currently, we are working on developing aqueous polyurethane dispersions with cationic stabilisation and hope to make them available to our customers shortly. At the moment, no other Russian manufacturer offers these materials.
Last year, HOMA announced the construction of new chemical and processing lines for polymer dispersions and adhesives in Nizhny Novgorod Region. This year saw the launch of a new line there for acrylic polymer dispersions used as a basis for adhesives and paint and coating materials. In five years, you expect to seriously expand the feedstock production for adhesives, paints and coatings, and paper and packaging. Plus, you are planning to move your production facilities from Moscow Region to Dzerzhinsk. What is driving this expansion?
The sanctions imposed on Russia have opened plenty of opportunities to national chemical manufacturers. With foreign producers leaving the market, opportunities have emerged for local companies to fill the opened niches in some segments. The Ministry of Industry and Trade has also stepped-in with wide-ranging support measures for the national industry. The government has provided us with a concessional loan on very favourable terms. In turn, we have committed to expand production volumes and contribute to the import substitution effort. The government support comes with stringent requirements, but they are spelled out in transparent and well defined terms and are easy to work with. While potentially, there could be some difficulties resulting from feedstock price volatility, we still have no doubt that our products supported by the import substitution programme will be in high demand.
HOMA R&D Сentre. Photo by HOMA.
As we proceeded with our modernisation plans, we realised that it would make sense to locate all our production capacities at one site and decided to move our Moscow Region facilities to Dzerzhinsk. The move helped cut significantly our logistics and production costs as our lines are mostly supplied by SIBUR's production site in Dzerzhinsk. The second factor behind the relocation decision is the availability of qualified workforce. Since Soviet times, Dzerzhinsk has been known as the capital of the country's chemical industry. The city is home to two dedicated universities, as well as a number of specialised colleges and vocational schools that provide the industry with well-trained personnel.
In 2018, after visiting a HOMA production site, President of Toyota Engineering Corporation Toshihiro Yamada said that the rate of lean manufacturing implementation at the site was the highest among the companies taking part in the Productivity Diagnostics for Russian Companies programme.
Could you tell us about your experience implementing lean production techniques at your facility?
Our experience with lean manufacturing goes back to 2010, when we invited a consultant from Toyota Engineering Corporation (TEC), specialising in implementing lean production systems across the world. We were primarily interested to see whether Toyota’s principles could be applied to a production line based on a continuous chemical process as opposed to a conventional conveyor. The consultant worked with us for only four days, but it was sufficient to make a profound impact on the company and our future development.
We already had a core group of staff consisting of approximately 30 specialists of various rank and occupation, including senior managers and regular personnel. The TEC expert shared with us the key principles of the Toyota system, which we immediately started to implement in our production process.
Our first priority was to adopt 5S, a workplace organisation concept, and I believe we did quite well. We then proceeded to introduce kanban, a tool that helps optimise internal organisation and supply system. We have implemented the poka-yoke system to prevent human caused product defects. We have also deployed the SMED rapid changeover system.
However, it does not always work as intended due to the specifics of chemical production that makes it all but impossible to convert the manufacturing line without stopping the chemical process. Recently, we have introduced the Total Productive Maintenance (TPM) system, which focuses on keeping all equipment in top working condition. For us, the key concept has been the pull production. Facing serious shortages of warehouse space, lean principles have been central in our efforts to better organise our production and logistical processes. We store no more than twice the minimum volume for each feedstock variety, and we produce no more than our immediate sales plans require. This is the key principle that we follow in our operations.
The lean manufacturing philosophy provides endless opportunities for self-improvement, meaning that there is still plenty of work to be done. I believe that SIBUR’s production system is the model that we should strive to emulate.
We have been working with SIBUR for over 7 years, it is our key feedstock supplier. We have built a strong relationship, as evidenced by years of successful cooperation.
HOMA R&D Сentre. Photo by HOMA.
I recently visited one of SIBUR’s production sites to attend an event organised by the company to share its H&S practices. I was really impressed by how efficiently things were organised there. This is true about SIBUR’s work in general. When we experience force majeure situations that require rapid response, SIBUR experts are always there, trying to analyse the problem and offer solutions that always end up helping to resolve the matter. SIBUR has a lot for us to learn from.
We used to think that Japanese and Russians have different mentality. However, as strange as it may seem, our experience has demonstrated that the best motivator is not material reward, but a person’s belief that his contribution is important and valued.
In 2019, HOMA joined the Labour Productivity and Employment Support programme, with the Company’s site in Nizhny Novgorod Region serving as a base facility for adapting the lean manufacturing principles to the Russian chemical industry. Could you shed more light on this?
Our involvement in the import substitution programme was quite successful, which prompted us to engage in other government-sponsored initiatives. This year we have joined the Labour Productivity and Employment Support national project, which aims to increase productivity in the medium and large business segment.
With regional competence centres created across the country, our Nizhny Novgorod centre turned out to be among the best by the level of expertise and activities it had to offer. Experts from the Ministry of Economic Development, the regional Ministry of Industry and Trade, and Rosatom Corporation as the programme’s major partner, help businesses to increase productivity, minimise feedstock losses and production costs, and shorten production processes.
The programme has two stages. Experts from Rosatom and the relevant Ministry visit the company and together with the company’s employees thoroughly examine one of the production lines, covering all processes from feedstock supply to end product shipment. Based on this analysis, a current state value stream map is created followed by expert assessment of the optimisation potential, including cutting the production time and introducing auxiliary processes. Experts work to determine the types and amounts of losses and shrinkage experienced by the company and draft a future state value stream featuring optimal production times, feedstock amounts, and labour.
A working group is set up comprising employees of various occupations, including managers, production engineers, logistics professionals, quality assurance specialists, customer care service providers, and skilled workers. The group works with external experts to identify major problems in the production process and propose relevant solutions.
HOMA R&D Сentre. Photo by HOMA.
The first stage of the programme lasts six months. First, there is a month-long training, followed by the value stream mapping activity, including the creation of the current state, ideal state, and future state value maps. The remaining time is spent on building and refining the production process. External experts rejoin the group toward the end of the six-month period to go over the training results, with members of the group defending their work.
Being part of the productivity programme provides the Company with significant benefits such as concessionary low-interest financing for up to five years. However, it also imposes a number of obligations, including a 10% production increase by the year's end for the line that was involved in the optimisation scheme. Additionally, the Company has to ensure an annual 10% production growth in 2020 and 2021.
In 2018, HOMA took part in the Productivity Diagnostics and Performance Enhancement project, provided by Japanese experts for Russian companies. Could you share some details about that project?
This is one of the Russian-Japanese initiatives, signed at the Eastern Economic Forum in Vladivostok. HOMA is one of the twelve companies that were lucky to be selected by Japanese experts to participate in this programme. At the early stages of the selection process, HOMA was visited by representatives from the Japanese Association for Trade with Russia and the Newly Independent States (ROTOBO). We showed them around our production facility highlighting major challenges, including those relating to research, new product launching and various managerial issues. Already at that stage, we were asked to choose the specialisation area of the experts we wanted to work with under this programme.
After we officially qualified for the programme, experts from Nomura Research Institute and Toyota Engineering Corporation (TEC) were sent to work with us. Imagine how surprised we were to see among them TEC President Toshihiro Yamada, a true legend of lean production.
Guest experts from Japan. Photo by HOMA.
In the course of the programme we had several meetings with the Japanese experts. Already during their first visit, they helped us draw up a comprehensive action plan to tackle the challenges we had outlined. Subsequently, they made some adjustments to the plan and helped identify some of the shortcomings in our work that complicated the solution of these problems. At the end of the programme, they conducted a final assessment of the Company, indicating the areas that needed further work and suggesting development strategies to focus on.
Recently we received a letter from Yamada-san saying that he is planning a trip to Russia with a group of experts and is ready to meet us and talk about the progress we have made. We are looking forward to the opportunity to meet him and continue our cooperation.
Lean manufacturing philosophy provides endless opportunities for self-improvement, which means that we still have plenty of work to do. SIBUR’s production process is the model that we should strive for.
What will change at the production site once the lean manufacturing practices are implemented? What results does the company’s management expect?
At the early stages of introducing lean manufacturing tools, we were able to increase our useful space by 30–35%. We have also cut our end-product warehouse stock by 2–2.5 times, reducing various feedstock inventories by 4–4.5 times without causing any shipment delays. This is quite an improvement for a production site measuring 10,000 sq m.
Even now, several years into lean manufacturing, we can add an extra 10–20 sq m of useful space by running a red tag campaign.
In fact, disposing of surpluses could be quite profitable. We made a substantial amount of money selling our surplus feedstock, construction materials and other stuff.
Using the SMED technology, we have reduced equipment downtime by 4–5 times during equipment changeover or repair work.
Lean manufacturing is based on active involvement of all staff members to ensure constant improvement of the production cycle. How do you manage to engage your personnel in this effort? How difficult a task is it?
We use two approaches. The first is a system of financial rewards to encourage employees to come up with efficiency enhancement proposals. Employees can claim a one-off bonus payment if their proposal is implemented or an increase in annual salary if the proposal generates constant economic effect. On top of that, we have so-called Kaizen groups for those enthusiasts who are always looking for ways to contribute to the improvement process by making their workplace more comfortable and convenient, optimising routine processes, enhancing labour efficiency, and through a variety of other means.
Production at HOMA. Photo by HOMA.
We used to think that Japanese and Russians have different mentality. However, as strange as it may seem, our experience has shown that the best motivator is not material reward, but a person’s engagement and belief that his contribution is important and valued. We believe that Kaizen groups have produced better results than the financial rewards scheme.
Today, training in lean manufacturing is mandatory for our new hires. During the trial period, they are supposed to read certain required texts on Kaizen groups and the Toyota manufacturing process. To pass the qualification test following the trial period, the new hires not only have to be familiar with these important works, but also be able to use analytical control tools, identify losses and find ways to eliminate them. They also need to present a research project featuring proper analysis and demonstrated economic effect. We approach this training very seriously, and quite often people fail their attempt at it having to retake it.
Download PDF