Recycling plastic as part of responsible production and consumption cycle is becoming a mark of civilised society around the world. According to the European Commission’s 2018 Strategy for Plastics, all plastic packaging should be recyclable by 2030.
Socially responsible companies strive to ensure their activities use a certain percentage of recycled materials. Faced with the influence of the global eco trend, the Russian market structure is changing before our very eyes
The COVID-19 pandemic has forced the world to take a fresh look at the use of plastic, and it has revealed the huge role that plastic products play in personal hygiene. Scientists have established as early as 2012 that single-use bags reduce the risk of catching a viral disease by 25%, but only a serious threat made humanity wake up to this fact. More recently, plastic tableware and packaging have been vigorously phased out in Europe and the United States, but now attitudes towards them, both among consumers and legislators, have radically changed.
Suppliers and retailers are rapidly rolling back to safer plastic packaging. Thanks to modern recycling methods, plastic packaging has actually become even more environmentally friendly than paper. Yandex.Lavka is a good example of this: after weighing up the carbon footprint, scope for recycling and hygienic safety of various types of packaging, the service ditched paper bags in favour of plastic ones. Furthermore, many cement manufacturers are abandoning paper bags for their products in favour of polypropylene bags. In addition to their ease of use, lower price and higher quality, they are much easier to recycle.
The last few years have seen a boost in domestic recycling: the state has recognised the area as a priority, and appropriate amendments have been made to existing legislation. The Strategy for the Development of Industry for the Sorting, Recycling and Treatment of Waste for the Period Until 2030 was passed in 2018. The whole idea of recycling has become an essential component of business policy for Russian majors. Socially responsible companies strive to ensure their activities use a certain percentage of recycled materials. Faced with the influence of the global eco trend, the Russian market structure is changing before our very eyes. Recycling is no longer just a business style, but is step-by-step becoming an industry in its own right. This new and promising direction has driven demand for the development of infrastructure and the search for cutting-edge, breakthrough solutions for the young recycling industry.
Attitude to plastic is being reconsidered.
A unique solution
Recycled plastic can be split into two key types: PIR (Post-Industrial Recycled) and PCR (Post-Consumer Recycled). PIR is the waste obtained fr om mechanical processing during production. On the whole, all of it goes to be recycled. The much more problematic category is the second: PCR is the plastic that gets thrown into the bin. It requires additional processing: it must be washed and have odours removed, before being sorted by material and colour, only then does it become suitable for recycling. Additional labour, developed infrastructure, and a conscious end user are all needed for it to be processed correctly. The most important task facing us today is incorporating this material into processing.
SIBUR announced a new project: the creation of plastic produced from landfill waste using PCR technology
SIBUR is one of the most successful players in this area. Last year, the Company began actively exploring whether recycled materials could be used in areas like blow moulding, injection moulding and film production. Recently, SIBUR announced a new project: the creation of plastic produced fr om landfill waste using PCR technology. Paint buckets made from the new material have already passed the first round of testing, which was ran by our R&D centre, SIBUR PolyLab, and Jokey, the world’s leading manufacturer of plastic containers. Architectural coatings and anti-viral paints under the O3 brands TRIOPRO™ and M2 will be produced in packaging using the SIBUR PCR compound as early as the second half of 2021. Looking ahead, it will be used for the production of containers for other products from O3, which manufactures protective materials, paint coatings, disinfectants and detergents (O3’s subsidiary O3-COATINGS is a ZapSibNeftekhim partner). This project was the first time a Russian company manufactured packaging using recycled plastic from landfill. As such, this compound is currently unrivalled on the domestic market.
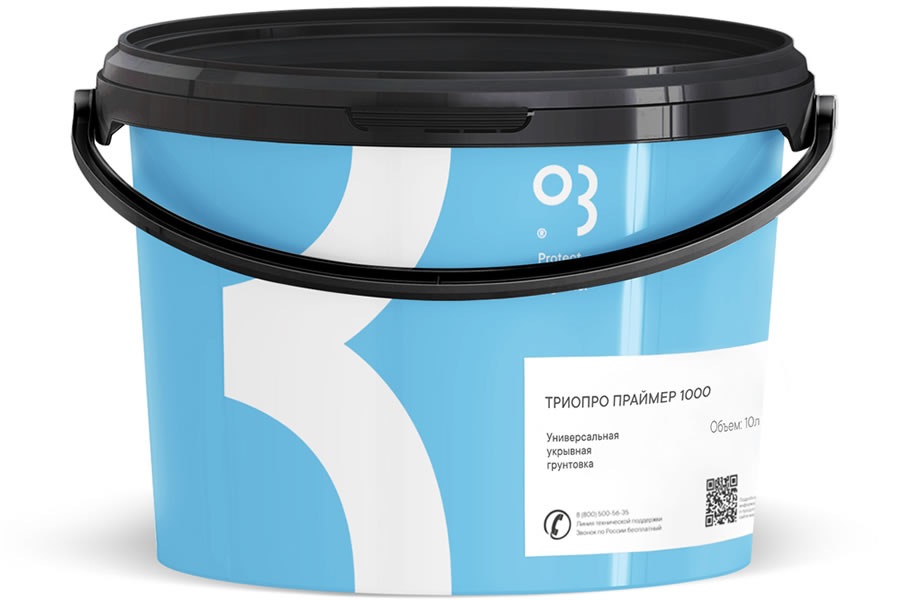
O3 products are packaged using the SIBUR PCR compound, which was developed by the PolyLab R&D Centre.
Irina Garustovich, General Director at O3-COATINGS:
“Under O3’s long-term development and carbon footprint reduction strategy, we will only be producing water-based materials in recycled plastic packaging from 2020. O3 and SIBUR PolyLab’s partnership allowed us to develop a truly green solution – packaging produced using PCR materials that can be recycled in the future.”
There is an acute shortage of feedstock on the market, as the waste collection and sorting system still has teething problems that need to be worked out
Elena Maltseva, Senior Expert, Product Marketing at SIBUR LLC, explained that the new compound – a mixture of virgin and recycled plastic – was developed at PolyLab. The material’s characteristics meet the stringent requirements of the brands who use it. The key benefit of these compounds is that recycled products can be used without compromising on the quality expected of virgin polymers. This is the safe solution that the Russian market has been waiting so long for: a product that is stable and predictable on the production line and fully meets the stated characteristics.
Valery Putikov, Sales Director at Jokey in the CIS:
“Cooperation between all responsible players in industry, trade, politics and civil society represents the only route to progressive improvements in the environmental situation and sustainable development. We always keep a long-term mindset and believe that entrepreneurial success is based on three pillars: economic growth, social responsibility and environmental balance.”
Owned infrastructure
The ongoing commercial production of a compound containing recycled polymers requires an uninterrupted supply of landfill waste. In turn, building up logistics chains exacerbates the need for appropriate infrastructure to be developed. At the moment, we are still at the formation stage, and there is an acute shortage of feedstock on the market, as the waste collection and sorting system still has teething problems that need to be worked out. In response, we decided to independently build a supply chain to get high-quality feedstock in the right volume. Perhaps that explains why SIBUR is the only Russian company that has managed to implement this kind of project.
Bottles made of virgin SIBUR PET, suitable for recycling and reuse.
Maxim Brodovsky, CEO, AZIMUT Hotels:
“In spring 2020 we partnered with SIBUR on PLASTIC – RESOURCE, NOT WASTE, a joint environmental project. Its goal is to develop the recycling of hotel supplies and, as a result, significantly cut down on the amount of waste polluting the environment. We have replaced cosmetics and accessories with more eco-friendly alternatives suitable for recycling at 10 hotels of our chain, and some of them are already made using SIBUR’s recycled plastic. First and foremost, we have swapped out the caps from our bottles of shampoo, shower gel and body lotion, but our bottles made of virgin SIBUR PET are still suitable for recycling and reuse.
On top of this, we collect waste plastic, which is sent for sorting and recycling. Looking ahead, we will use this recycled material to produce thousands of warm vests, fleece blankets, the filling of jackets and many other useful things. In just one year, we have collected more than 3.6 tonnes of waste plastic. Our hotel guests appreciate this environmental initiative and voice their support for it.”
The key trends that will be in demand over the coming decades are caring for nature and reducing the negative impact on the environment. They are clearly the key drivers behind the development and implementation of not only new technologies, but also business processes in companies
Outlook
“Right now, we have a solution for blow moulding, films and injection moulding. The final product is produced according to our unique blend of virgin and recycled plastics. For each type, we have developed our own composition of feedstock. For injection moulding, this is recycled polypropylene, for blow moulding and films, it’s recycled polyethylene. Three different products rally around a common goal – the production of a compound that contains landfill waste. Our partnership with Jokey has become a kind of pilot for the Company. SIBUR’s experts are also running tests on the same product with other processors. In the future, it could be used to produce packaging containers and various consumer goods – buckets, hangers, etc. – but for now we are focusing on launching a recycled compound for blow moulding, for example bottles and cans for household chemicals and automotive oils,” says Elena Maltseva.
The material that the Company currently offers will enjoy a wide application in the production of packaging for varnishes, paints and mixtures, as it is an area wh ere the use of recycled material obtained by mechanical recycling is allowed. However, this solution is not suitable for the food and cosmetics industries, which have much more stringent requirements for the quality of packaging materials. For this area, we must look to build up the capabilities of chemical recycling. It is a more complex and expensive method, and European manufacturers are currently conducting active research into it. SIBUR’s experts are also exploring how far it could be implemented in Russia. They predict that implementation period of this kind of project would be around three to four years, and that it would allow major brands to use even more recycled material in the production of their packaging.
In parallel with fostering relationships with its own partners, SIBUR implements industry-wide projects, as the industry requires comprehensive solutions. The Company recently launched re.actor, an online marketplace linking waste generators and recyclers. The site has around 5,000 users, and every month about 1,300 ads are posted to sell used plastic, waste paper, metal, glass, and textiles.
The key motivation
When new environmental practices are introduced, they are always associated with additional obligations and the need to address certain problems. For example, it is not yet possible for PCR packaging to be cheaper than virgin plastic packaging in Russia, since its cost includes collection, sorting, logistics, washing, further sorting by colour, transportation to processing, the production of the raw materials themselves, yet more transportation to the manufacturer, and so on.
What is driving companies to implement sustainable solutions and, in particular, to use recycled polymers?
“The global food system of today is more effective than ever before at providing a huge number of people with affordable food and putting a smile on their face; yet, it may soon be faced with challenges that threaten its ability to meet the needs of a growing global population,” explains Irina Semenova, Communications Manager at PepsiCo Russia and BUCCA.
“In an efficient food system, packaging makes high-quality products available to everyone, extends their shelf life and helps reduce food waste. Plastic packaging is convenient to use and allows us to preserve the taste of the product, while getting it to the consumer safely. On the one hand, modern technologies allow packaging to be made as environmentally friendly as possible, on the other hand, they ensure that it is almost entirely recycled.
PepsiCo is committed to ensuring that plastic never ends up as litter or landfill. Our goal is to make 100% of our packaging recyclable, compostable or biodegradable by 2025. At PepsiCo, we believe that it is possible to change the way the world produces, delivers, consumes, and disposes of food and beverages to address the challenges facing the modern world, together.”
All PepsiCo packaging will be recyclable, compostable or biodegradable in the near future.
“In line with its 2025 strategy, O3 adheres to the principles of safety and environmental friendliness when developing all products and materials,” says Gregory Shifrin, CEO at O3 Company. “O3 has plans to not only mass-produce PCR packaging, but also to place special containers at points of sale for collecting used packaging, ready to be sent for further processing. The output packaging will be 40% more expensive than its virgin plastic counterpart, but O3 believes that the initiative will find demand among consumers and under the norms of Russia’s environmental policy.
The green trend seen in the production of environmentally friendly materials now extends to all stages of the production cycle. The key trends that will be in demand over the coming decades are caring for nature and reducing the negative impact on the environment. They are clearly the key drivers behind the development and implementation of not only new technologies, but also business processes in companies. The introduction of new eco-friendly products to the market will satisfy the needs of more demanding customers, who are increasingly thinking about wh ere, how and fr om what their packaging is made. This is what motivates O3 to develop and implement new breakthrough materials and technologies, and to use sustainable solutions such as recycled polymers.”
The chemical recycling is a more complex and expensive method, and European manufacturers are currently conducting active research into it
“At Danone, we strive to create and use 100% recyclable packaging and produce it responsibly. We are aware of the need to reduce the negative impact of production on the environment and are already rolling out green initiatives to curtail our impact. All of our packaging will be recyclable, reusable or compostable by 2025,” says Vasily Fokin, Head of Sustainability at Danone in Russia and the CIS. “We constantly look to improve our business processes and strive to switch to more environmentally-friendly types of plastic: we have already abandoned PVC (SPI code 3), we are working on a complete phase-out of polystyrene by 2025, and we are increasing the share of more eco-friendly PET in our packaging.
We launched a number of green initiatives in 2019, for example, Green Cities, Russia’s first-ever closed-cycle collection and processing project for packaging containers, as well as a range of educational courses on sustainable development, healthy nutrition and responsible consumption for consumers. We are also running a pilot to replace plastic straws and switch packaging materials with more eco-friendly types of plastic.
Danone handles both its own production waste and consumer packaging waste, and fulfills its extended producer responsibility obligations. Even today, we already use recycled plastic in packaging production; for example, we launched a pilot project in 2020 to use 45% of recycled PET in a number of brands. We also use recycled plastic in HDPE packaging, which allows us to reduce our impact on the environment.”
A waste collection point for recycling in Ufa.
“The use of recycled materials is very important for IKEA. We analysed our negative impact on the planet and realised that the use of virgin materials in the production of our products is actually wh ere the biggest impact lies. We want to reduce this impact and are already doing it by cutting down on the amount of materials we use, and by replacing virgin materials with recycled ones,” highlight representatives of IKEA in Russia.
Download PDF
PepsiCo
“Our goal is to make 100% of our packaging recyclable, compostable or biodegradable by 2025.”